O 引言
选区激光熔化(SLM-Selective Laser Melting)是金属件直接成型的一种方法,是快速成型技术的最新发展。该技术基于快速成型的最基本思想,即逐层熔覆的“增量”制造方式,根据三维CAD模型直接成型具有特定几何形状的零件,成型过程中金属粉末完全熔化,产生冶金结合。
利用选择性激光熔化激光快速成型技术进行复杂金属零件的制造,其制造结果能否满足实际要求,其中一个很重要的方面是尺寸精度与形状精度能否满足要求。
l 影响成型件尺寸形状精度的主要因素分析
(1)激光光斑大小
在其它参数一定的情况下,激光光斑大小对尺寸精度会产生较大的影响,假定其激光能量足够熔化金属粉末,不产生球化现象,激光光斑越大,则尺寸误差越大,反之则误差减小。分析原因:因为快速成型系统中采用的加工路径是线扫描路径,即把加工面看成是线的集合,如果光斑是一个点,则加工实际轮廓和理论轮廓重合,但由于激光光斑具有一定的大小,因此,如果加工如图1所示的零件,则它的外环轮廓和内环轮廓会比理论轮廓大或者小一个光斑半径,实际加工轮廓如图1中虚线所示。
图1 光斑影响加工尺寸误差示意图
另外,光斑的实际大小还受激光功率和扫描速度的影响。当速度恒定时,功率越大,光斑越大,尺寸加工误差越大;而与之相反,当功率恒定,扫描速度增大时,尺寸误差减小。因为扫描速度增大,则单位面积激光能量密度减小.激光熔池尺寸减小,相当于减小了激光功率。
(2)铺粉层厚和搭接率
随着单层层厚的增加,尺寸误差增大。层厚增加,需要熔化的粉末增加,要能达到成型要求,则必然要增加激光功率,所以成型件尺寸精度下降。
如图2所示,在加工倾斜面时,当倾斜角度a一定时,如果层厚H增加,则相邻两层的错切量△L增大,从而影响斜面的形状精度。
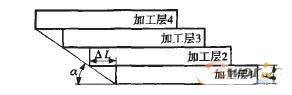
图2层厚对斜面成型精度的影响
搭接率的大小直接影响成型件的轮廓精度。如图3所示。当采用光栅扫描填充,光斑直径一定时,搭接率越小,则轮廓成型精度越低。
图3搭接率对轮廓精度的影响示意图
(3)金属粉末的粒度,直接影响铺粉层厚,粒度增大则铺粉的最小层厚增加,成型件的尺寸误差增大。另外,当激光扫描线落在金属粒子边缘时,金属粒子受光部分被溶化,使金属粒子被焊接在零件上,形成凸凹不平的毛刺。
(4)铺粉设备的精度
根据成型原理,SLM铺粉设备的精度直接影响加工制造精度。在铺粉设备的误差中,特别重要的是铺粉过程中的刮板与基板之间的间隙误差,因为这个误差最终影响铺粉厚度的均匀性。间隙误差是一种累积误差,影响的因素较多,也较复杂。主要包括:①刮板刃口的直线度;②刮板直线往复运动的跳动;③成型缸活塞上下运动时的摆动与转动;④基板平面与推动丝杠轴线的垂直度。其中成型缸的转动误差对刮板与基板之间的间隙不产生影响,只对成型件的形状精度有影响;而刮板刃口的直线度误差则直接影响刮板与基板之间的间隙大小。
2提高SLM快速成型件尺寸形状精度的途径
针对以上影响因素,可以通过以下途径提高成型件的精度:
(1)在满足加工要求的前提下,尽量减小光斑直径和层厚。
(2)实验证明:在考虑加工效率的前提下,搭接率取30%一50%时,成型件精度一般可以满足实际要求。
(3)在满足加工要求和加工效率的前提下,选择合适的功率和扫描速度。
(4)对于图1所示的问题,可以通过软件控制,采取轮廓偏置的方法来解决。即将外环轮廓向内偏置一个光斑半径,将内环轮廓向外偏置一个光斑半径,而光栅填充要以偏置后的轮廓为基础来进行。
(5)严格控制铺粉设备的精度,
利用导向套筒加长(约为导杆直径的3—5倍)和提高配合精度等级等措施可以较好的消除成型缸活塞上下运动全程的摆动误差。
采用高精度的线性模组可以消除刮板直线往复运动的跳动误差。
利用基板水平调节装置可以清除基板与丝杠轴线的垂直度误差,如图4所示。
图4基板水平调节装置实物图
3 尺寸与形状精度的评价方法
3.1 评价方法
逆向工程,也叫反求工程,实物反求技术是利用仪器去收集物体表面的几何数据;然后再利用软件,计算出采集数据的空间坐标;最后用专门的软件,把三维数据拟合成表面模型,得出实物的i维模型。
图5所示是用SLM快速成型方法制造的金属可摘除局部义齿支架实物图,材料为Fe一17Cr-4Ni.2Mo-0.1C。可摘除局部义齿支架是人体口腔修复的重要辅助工具。由于它的表面是形状复杂的曲面,所以用常规方法难以精确评价它的形状和尺寸精度。本文用逆向工程的方法进行评价。具体如下:
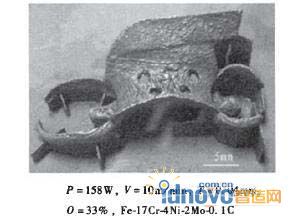
图5金属可摘除局部义齿支架实物
(1)物体数据化:采用柯尼卡美能达RANGE7采集物体表面的空间坐标值。柯尼卡美能达RANGE7是一款高精度的非接触式三维扫描仪,主要功能是扫描三维物体,以获得其外形三维尺寸数据。
(2)物体三维模型重建:RapidForm是韩国INUS公司开发的全球四大逆向工程软件之一,它可实时将点云数据运算出无接缝的多边形曲面,得出实物的三维模型。由RapidForm重建图5所示的零件,结果如图6所示。
图6 金属可摘除局部义齿支架三维重建
(3)利用Rapidform软件进行设计数据与扫描数据的全局拼接比较,如图7所示,图中左边模型为可摘除局部义齿支架CAD模型,右边为三维重建后的模型。软件通过对比扫描数据和三维CAD设计数据,自动导出检测报告,包括全局误差以及几何尺寸误差。
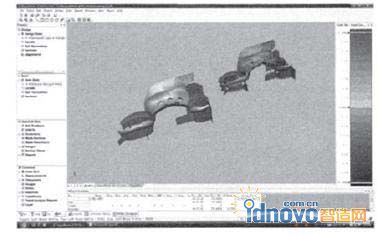
图7原始CAD模型与重建CAD模型比较
3.2结果与分析
如图8所示,将CAD模型和三维重建模型进行重叠对比,以不同颜色来显示零件各处是否存在加工偏差及偏差的大小范围。偏差的大小范围用不同的颜色来表示,按图7右边的色彩设置,说明如下:
图8原始CAD模型与重建CAD模型重叠拼接后的结果图
(1)设置的偏差范围为±1mm,如果偏差值大于+1mm则以深红色显示,如果偏差小于一1mm,则以深蓝色显示:
(2)如果偏差为0mm,则显示为绿色;
(3)如果偏差在0—1mm之间,显示颜色在黄色和红色之间变化,偏差值增大,颜色变深;
(4)如果偏差在一1一0mm之间。显示颜色在深蓝色与浅蓝色之间变化,颜色越深偏差越大。
从图8可以清楚地看到:第一,没有深红色及深蓝色存在,说明偏差值均在±1121121之间,第二。图中绿色面积较大,只有极小部分是黄色与浅蓝色,说明三维重建后模型与CAD模型比较,部分是吻合的,没有偏差,即使有偏差的地方,颜色也比较浅,故偏差值也较小。
软件通过对比分析得出其尺寸与形状误差结果,如表l所示。
表1全局偏差测量结果表
从表l可知,测量结果中,偏差最大值为0.959mm,平均偏差为士0.172mm。
三维测量结果与原始CAD模型的吻合结果如图9所示。
图9形状与尺寸精度分析结果图
通过对113363个点的偏差进行统计,得到各个偏差范围内的点的个数占总点数的百分比如表2所示。利用SLM技术制作的可摘除局部义齿支架与原始模型在偏差为±0.285mm范围内的吻合度可达到75.95%.可见其加工精度比较高,在此基础上,再进行一定的辅助后续精加工,完全可以得到满足实际使用要求的可摘除义齿支架。
表2各个偏差范围内点数占总点数的百分比表
4 结束语
本文首先分析了影响SLM快速成型件尺寸形状精度主要因素,以及提高成型件精度的方法;然后针对以上常规精度评价方法的不足,以可摘除局部义齿支架为例,利用逆向工程的方法对零件的形状尺寸精度进行评价,取得较好的评价结果。
相关文章
- 2021-09-08BIM技术丛书Revit软件应用系列Autodesk Revit族详解 [
- 2021-09-08全国专业技术人员计算机应用能力考试用书 AutoCAD2004
- 2021-09-08EXCEL在工作中的应用 制表、数据处理及宏应用PDF下载
- 2021-08-30从零开始AutoCAD 2014中文版机械制图基础培训教程 [李
- 2021-08-30从零开始AutoCAD 2014中文版建筑制图基础培训教程 [朱
- 2021-08-30电气CAD实例教程AutoCAD 2010中文版 [左昉 等编著] 20
- 2021-08-30电影风暴2:Maya影像实拍与三维合成攻略PDF下载
- 2021-08-30高等院校艺术设计案例教程中文版AutoCAD 建筑设计案例
- 2021-08-29环境艺术制图AutoCAD [徐幼光 编著] 2013年PDF下载
- 2021-08-29机械AutoCAD 项目教程 第3版 [缪希伟 主编] 2012年PDF