引言
激光表面微造型技术(LST)以其加工速度快、对环境无污染和良好的可控性等特点尤为引人注目,利用该技术在摩擦副表面加工出的微观形貌,可起到动压润滑、储存润滑油以及收集磨损颗粒等作用。与此相适应,先后有学者就机械密封、缸套/活塞环以及推力轴承等表面的激光微造型技术开展了大量研究,发现微造型形貌可以有效地改善表面润滑、增强抗磨效果。然而相关研究主要集中于面接触摩擦副表面,对于凸轮/滚轮副这种线接触方式的表面几何形貌同摩擦学性能之间的关系研究较少。本文选用淬火-回火45号钢作为试样材料,模拟油泵凸轮工况(低速重载),考察油润滑状态下各种造型形貌对45号钢表面摩擦磨损性能的影响。
l 实验方法
1.1试件及表面形貌
将尺寸为29mm×20mm×8mm的45号钢试样用砂纸打磨并进行抛光(表面粗糙度达到R0.1),在二级管泵浦Nd:YAG激光器上对抛光面进行激光微造型处理,采用声光调Q控制产生脉冲激光,激光波长为532 nm,功率密度在107 W/cm2 左右,重复频率在5-15 kHz,得到凹坑、断续槽、交叉网纹等14种表面形貌。WKYO-NT1100型表面微观几何形貌测量仪测得的激光微造型45号钢试样表面三维形貌如图1所示。变化这3种基本形貌的组合和几何参数,构成试样表面不同的造型方案,各种造型形貌示意图及几何尺寸如表1所示。
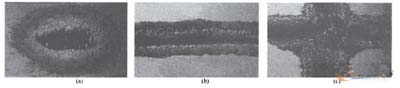
图1激光微造型试样表面的三维实体形貌图
表1激光微造型试件表面形貌、几何参数、磨损量
1.2实验方法
实验研究线接触油润滑状态下,多种激光微造型形貌对45号钢表面摩擦磨损性能的影响,选用UMT-2型摩擦磨损实验机的销盘实验装置,如图2所示,滚轮和盘沿箭头所示方向相对运动。上试件选用西17mm×9mm的合金铸铁滚轮(滚轮周向对称开有3个螺纹孔3-M6×0.75-6H,钻深7mm,攻深5mm,相邻两螺纹孔中心线夹角120°),并通过标准件销(下端加工有部分螺纹)与实验机相连,硬度为58~62HRC,滚轮材料成分如表2所示,下试件为29mm×20mm×8mm的激光微造型试样或未经激光处理的光滑试样,材料精选含碳量为0.42%~0.47%的45号钢,经淬火一回火处理,硬度42~48HRC。实验中上试件固定,下试件做往复运动,往复行程为6mm。利用传感器在线检测接触面间的载荷和摩擦因数,并通过电脑输出数据。实验所用润滑油为GL-585W/90重负荷车辆齿轮油,相当于GBl3895--1992。粘度等级符合美国SAE 85W/90标准。
图2摩擦磨损实验示意图
表2合金铸铁的成分
实验步骤:①对每个试样在线磨合,以保证上下试样沿滚轮接触宽度方向基本为均匀线接触。②将试件在丙酮中超声清洗20 min后晾干待用。③将晾干的试样在电子天平上称量,并做好记录,电子天平测量范围0-100g,精度为0.0001g。④实验前在接触区域滴加0.2mL的润滑油,实验开始后每10min加油一次,以保证上下接触面间始终处于富油状态。⑤实验温度为室温20℃,通过上试件加载,施加载荷147 N(允许加载的极大值),下试件往复运动的平均线速度为0.04m/s,每个试样在线磨合30 rain。⑥实验结束后,再次对试件进行超声波清洗和称量,并对前后两次的质量进行对比。实验结束后利用扫描电子显微镜(SEM)分析试件的磨损表面,并对表面磨痕及轮廓形状进行测量。
2结果与讨论
2.1耐磨性
摩擦磨损实验中各激光微造型试样和光滑45号钢试样表面的磨损量如表1所示。可以看出,各种激光微造型试样表面的磨损量皆低于光滑试样表面。分析其原因,一方面可能由于微造型形貌可在上下表面问产生一定的流体动压润滑效果,将上下接触面分开;另一方面由于凹坑或凹槽可以起收集磨损磨粒的作用,从而减少了接触面发生磨粒磨损现象的几率。此外,骤冷骤热的激光加工过程,还会引起造型区域表面的材料微观组织变化,形成具有高硬度和超细组织的硬化层,也在一定程度上提高了45号钢试样表面的耐磨性能。
2.2抗擦伤性能
实验中观察到:光滑试样15在磨合后期表面出现冒白烟现象,而激光微造型试样1-14在磨合过程中未观察到白烟现象。图3给出了光滑、微造型试样磨痕表面形貌SEM照片,可以看出,光滑试样磨痕表面呈现较为严重的粘着、擦伤和疲劳脱落迹象(图l0a),而激光微造型凹坑和凹槽试样磨痕表面的粘着、擦伤和疲劳脱落现象相对较轻(图10b、l0c、10d)。据此可推测,经过激光微造型处理后,45号钢试样表面的凹坑、凹槽等结构,更有利于改善表面减摩和抗磨效果,从而显著提高激光微造型处理表面的抗擦伤能力。
图3扫描电子显微镜下光滑型和激光微造型试件
2.3摩擦学性能
图4示出了几种形貌参数各不相同的凹坑(表1中试样1~6)表面的摩擦磨损性能测试结果。可以看出,除试样1、2外,同光滑表面相比,带凹坑的试样表面摩擦因数较小。也就是说,线接触时,在富油的情况下,表面的凹坑能起到一定的减摩效果,文献[11~12]中针对面接触形式也有过类似结论。
图4凹坑及光滑试样表面的摩擦因数
试样1、2表面的摩擦因数比光滑表面增大的原因:一方面试样1表面凹坑的面积占有率过大,高达38.5%,而试样2表面凹坑形状很不规则(图5),另一方面可能由于凹坑深度过浅;这些都对其表面摩擦因数的增大有影响。试样3、4、5、6四种凹坑试样的深度从浅到深为:试样3、试样4、试样5、试样6,它们的摩擦因数从大到小为:试样6、试样3、试样4、试样5。可以看到,凹坑不宜过深也不宜过浅,过深或过浅的凹坑都会引起接触表面摩擦因数的增大。在一定范围内摩擦因数随着凹坑深度增大而减小,但是有一个最佳值,结合实验结果可知此最佳值为15um左右。

图5试样2表面的微凹坑形貌
图6是交叉网纹、交叉短线和凹坑组合形貌以及光滑表面的摩擦因数。可以看出,网纹表面的摩擦因数与未处理的光滑表面基本相等,而交叉短槽与凹坑的组合形貌表面摩擦因数远高于光滑表面,但都比光滑表面更平稳。Pettersson等也曾针对面接触摩擦副指出凹槽或网纹等形貌表面的摩擦因数比光滑面波动小,但大小相同。文献[13]中针对微造型铸铁表面也有相似的结论。
图6网纹、组合形貌和光滑试样表面的摩擦因数
图7为0°~90°(与滑行速度方向夹角)断续槽及光滑试件表面的摩擦因数。可以看到,凹槽试样表面的摩擦因数比光滑表面均显著增大(45°断续槽表面略有下降),但相对光滑表面较稳定。这说明在线接触油润滑状态下,不论是贯通的或是断续的凹槽,都会增大表面摩擦。究其原因,一方面润滑油顺沟槽流走,造成了造型区域局部低压区,使表面油膜变薄,另一方面,在线接触油润滑条件下,断续槽造型使原本光滑、平坦的试样表面形成了富有规律的凹凸不平状搓板纹,增加表面粗糙度的同时,增大表面摩擦阻力。此外,在0°-90°断续槽试样中,30°断续槽试样表面的摩擦因数随时间不断下降,并在1600S时降到光滑表面以下,45°断续槽试样表面的摩擦因数较光滑表面显著减小,因此推测斜度在30°~45°之间的断续槽造型具有一定的减摩效果,且越接近45°减摩效果越好。
图7断续槽和光滑试样表面的摩擦因数
3 结论
(1)与光滑试样相比,激光微造型试样表面的耐磨性和抗擦伤性得到提高。
(2)在线接触油润滑条件下,表面凹坑对润滑的减摩效果明显,而凹槽效果相反。
(3)凹坑深度和断续槽的斜度各有一个最佳值,深度或斜度在这个最佳点附近,减摩效果最好。
(4)不论是凹坑、凹槽或是其组合形貌造型表面,它们的摩擦因数均比光滑表面稳定得多。
相关文章
- 2021-09-08BIM技术丛书Revit软件应用系列Autodesk Revit族详解 [
- 2021-09-08全国专业技术人员计算机应用能力考试用书 AutoCAD2004
- 2021-09-08EXCEL在工作中的应用 制表、数据处理及宏应用PDF下载
- 2021-08-30从零开始AutoCAD 2014中文版机械制图基础培训教程 [李
- 2021-08-30从零开始AutoCAD 2014中文版建筑制图基础培训教程 [朱
- 2021-08-30电气CAD实例教程AutoCAD 2010中文版 [左昉 等编著] 20
- 2021-08-30电影风暴2:Maya影像实拍与三维合成攻略PDF下载
- 2021-08-30高等院校艺术设计案例教程中文版AutoCAD 建筑设计案例
- 2021-08-29环境艺术制图AutoCAD [徐幼光 编著] 2013年PDF下载
- 2021-08-29机械AutoCAD 项目教程 第3版 [缪希伟 主编] 2012年PDF