O 引言
激光打标机主要用于在金属、塑料等各种材料表面标刻划字符及图案,在许多行业中有着广泛的应用,如在产品上打出商标、出厂日期产品序列号等。与传统打标机相比,激光打标机属于非接触性打标,对工作面无压力,不会产生变形。对材料表面无污染、腐蚀,并且不需要任何耗材,有着广阔的市场前景。标刻质量和标刻深度是高性能激光打标机最重要的几项指标,对于激光打标系统的市场应用以及产品的标刻质量有着重要的影响。基于此,本文提出一个高性能标刻路径优化的解决方案。
激光标刻中,在加工设定的标刻图案时,激光束标刻行程之间以空行程连接,空行程即两条标刻路径之间关闭激光的那段路径。由于空行程时激光器是关闭的,因此使用任何方式运行空行程都是可行的。但空行程的行走却会直接影响到实际标刻图案效果,对空行程与标刻行程的连接优化是提高实际图形标刻后图形质量的一种非常必要的步骤。传统的空行程以前后相邻标刻行程端点的直线连接过渡。但由于控制激光束行径的振镜偏转镜片具有一定的转动惯量,这种过渡形式在高速标刻时会产生末段过冲和起始段侧移现象,特别是在标刻精细图案时比较明显。
在没有对空行程进行连接优化前,考虑到由于空行程不直接影响标刻效果,传统空行程采用前一条可行程的终点直接与后一条空行程的起点直线连接来过渡,如图1(a)。但是由于振镜系统的偏转镜片运行接近其最大加速度和最大速度的临界状态,由于加速度非常大,虽然空行程直线连接最短,空行程扫描所需时间能够减少,节约每一次的标刻时间。但是这样控制激光轨迹,则在实际振镜镜片摆动中由于振镜转动惯量的影响其激光运行轨迹会与预设轨迹有所偏差,这种情况下以临界加速度来行走空行程的一个问题是,会导致标刻路径的起点和终点处出现指向空行程方向的偏离。因此,采用让空行程在起点和终点处不再走直线,而是走一条起始方向和结束方向与对应实际标刻路径相切的曲线的方法来解决,同时能够保证振镜系统的偏转镜片运行接近其最大加速度和最大速度的临界状态并顺利过渡到标刻行程,如图1(b)所示。在标刻路径的插补计算上,采用速度规划的概念来整体性地提高标刻效率和标刻性能。
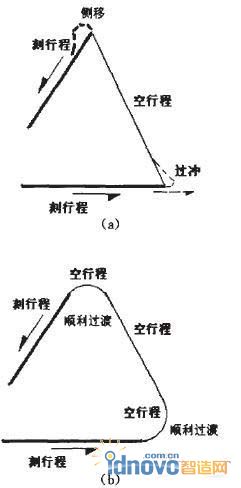
图1与实际标刻路径相切曲线过渡空行程
1 以切弧过渡连接标刻路径
在本文的算法实现中,定义的连接曲线是一段半径为固定半径R的圆弧再加一段直线段来描述。因为圆是一种最简单的二维曲线,它在数学上定义简单,在实际的曲线分段中也最容易实现,因此我们通过上述方法来实现曲线过渡是合理且可行的。
理论上每条标刻行程的相切圆都有两个,如图2所示。对前一条标刻行程来说,因为标刻行程受行走矢量方向的约束,该行程的相切圆必须在终点处,如图中B点,其半径为固定值R。对后一条标刻形程来说,该行程的相切圆必须在起点处,如图中C点,其半径也都为R。那么在实际计算中我们只需各选取相应标刻行程的一个相切圆来圆弧过渡即可,但是这四个相切圆的组合会有四种选取情况,在每一种选取情况下,两个圆的过渡路径在数学上又可能会有四种相切方式。那么如何取舍相切圆的选取,以及如何计算相切路径是一个很重要的问题。
图2两条标刻行程间四种切弧路径过渡
解决这个问题一个重要的原则,即使连接后的过渡曲线尽可能的短,来节约空行程行走时间。在实际的计算中,为了简单起见我们通常取圆心之间距离最短的两个相切圆。这样固定相切圆选取后,在数学上会有四条切线(如图3所示),其四条切线的计算过程如下:
图3两相切圆.之间四条切线的计算
在两条圆的切线的计算上,先给出切圆上如下相关定义:
r为两圆的半径;O1,O2分别为两圆的圆心;Vr为两圆心问的矢量,即Vr=O2一O1。
由以上定义可得出四条切线计算公式为
L1:(O1一rV1,O2一rV1),其中V1·Vr﹦0,并且| V1 |﹦1,从此式可得出V1有两个矢量满足条件,再通过V1×Vr≤0来限定V1的方向。同理,L2:(O1+rV2,O2一rV2)。
L3:(O1+rV2,O2一rV3,其中V2·Vr﹦2r,并且| V2 |﹦1,同上,V2也可能有个矢量满足条件,仍然通过V2×Vr≥0来限定耽的方向。
同理L4:(O1+rV3,O2一rV3),其中V3·Vr=2r,并且| V3 |=1,V3×Vr≤0。
以上四条切线都是从圆O1到O2的方向,但在实际的计算中也有可能计算出相反的方向,不过这并不影响后续的计算。由于前后相邻标刻行程是有矢量方向的,那么其每条切线与连接圆弧的走向必须与标刻行程与连接圆弧的走向一致,因为标刻行程其实也是一条切线,因此可描述为,两条切线相对于其相切圆圆心的转动方向一致。数学上有如下公式:
W1=V1×(O1一B)=V2×(O1一C),其中W1为转动方向也即两个矢量的叉乘积,V1为前一条标刻行程的矢量,O1为第一个切圆圆心,B为前一条标刻行程的终点,C为切线的起点,V2为切线的矢量方向。
W2=V2×(O2一D)=V3×(O2一E),其中W2为转动方向,V3为后一条标刻行程的矢量,O2为第二个切圆圆心,E为后一条标刻行程的起点,D为切线的终点,V2为切线的矢量方向。
在理论上,符合以上两个转动方向定义的切线有且只有一条,因为符合前一条标刻行程的四条切线中有两条切线的方向与W1的转动方向相反,那么过滤后剩余的两条切线中符合后一条标刻行程的两条切线的方向又只有一个与W2相同,一个与W2相反,那么过滤掉与W2相反的那条切线,最后只有一条切线符合上述条件,如图4所示。该条切线即最终所选取的切线。
图4根据转动方向一致原则只可能有一条切线过渡
2优化连接应用
利用VC++平台编程实现该优化算法模块并加入到华中科技大学快速成形中心的激光标刻软件PowerMarker系统后,载入一个PIT格式的纽扣标刻图案,其整体优化效果如图5所示,局部细节效果如图6所示。其中的深色(绿色、黑色、蓝色等)是标刻路径,白色是空行程。
图5 对纽扣标刻图案应用连接路径优先
图6 连接路径优化图案细节
在优化激光空行程路径后,采用全局速度规划的方法对所有标刻路径和空行程进行插补优化处理,使其在激光运行路径的任何位置处其加速度都不会超过振镜所能承受的最大加速度,达到振镜在对长路径行走的时候可以达到高得多的最大速度和平均速度效果。全局速度规划的思想为:根据加工曲线曲率半径的变化,实时改变插补步长,在曲率半径大的地方,采用大的速度,在曲率半径小的地方采用小的加工速度,只要速度变化均匀,不是突然上升或下降,加工速度可以随曲线的变化而变化。在插补过程中,每点速度取决于三个因素:(1)曲率半径,半径越大,速度越大,两者的关系由插补误差和振镜特性决定;(2)该点到路径终点的行走长度,保证能在终点处停止,不造成过冲;(3)振镜所容许的最大速度。对优化后激光运行轨迹的插补优化如图7所示,完全尺寸插补效果由于幅面原因没有放入本文。
图7空行程和刻行程的插补效果
利用该算法模块进行实验,在实验平台上,激光器采用50W的CO2:气体激光器。振镜系统采用美国Nutfield公司12mm镜片的二维振镜系统,标刻设备采用华中科技大学激光加工国家工程研究中心的纽扣机设备。在实验工艺中,连接圆的半径根据不同的标刻图案和振镜的具体性能来设置,目前采用的Nutfield公司的振镜,其镜片的最大速度可以达到lm/s。最大加速度可以达到10m/s,对于幅面在lOOmm×100mm以内的图案,根据实验其连接圆半径理论上需要5mm,而对于大多数幅面在10mm×10mm以内的图案其半径lmm即可。其各种图案的打标效果如图8所示。
图8 各种图案的打标效果
3 结束语
基于该路径优化算法的激光标刻软件Power—Marker(图9)已经在华中科技大学的HIS系列激光打标机上得到应用,与以往软件相比,消除了实际标刻中在起点、终点和尖点等处的轮廓失真、过烧等缺陷,标刻效率和标刻质量得到极大的提高。
PowerMarker软件运行界面
相关文章
- 2021-09-08BIM技术丛书Revit软件应用系列Autodesk Revit族详解 [
- 2021-09-08全国专业技术人员计算机应用能力考试用书 AutoCAD2004
- 2021-09-08EXCEL在工作中的应用 制表、数据处理及宏应用PDF下载
- 2021-08-30从零开始AutoCAD 2014中文版机械制图基础培训教程 [李
- 2021-08-30从零开始AutoCAD 2014中文版建筑制图基础培训教程 [朱
- 2021-08-30电气CAD实例教程AutoCAD 2010中文版 [左昉 等编著] 20
- 2021-08-30电影风暴2:Maya影像实拍与三维合成攻略PDF下载
- 2021-08-30高等院校艺术设计案例教程中文版AutoCAD 建筑设计案例
- 2021-08-29环境艺术制图AutoCAD [徐幼光 编著] 2013年PDF下载
- 2021-08-29机械AutoCAD 项目教程 第3版 [缪希伟 主编] 2012年PDF