SolidWorks是一套机械设计自动化软件,简单易学,机械工程师能快速地按照其设计思想绘制出草图,制作模型和详细的工程图。应用特征和尺寸,进行零件三维造型,三维模型除了可以将设计思想以最真实的模型在计算机上呈现出来之外,还可随时计算出铸件的体积、面积、质心、重量、惯性矩等,用以了解零件、模型的真实性。可随时对尺寸修正,相关的二维图形或三维实体模型均自动修改,同时装配、制造等相关设计也会随之变动,如此可确保数据的正确性,避免人为改图的疏漏情形,减少了工作时间与人力消耗。由于有参数式的设计,机械工程师可以运用强大的数学运算方式,创建各尺寸参数之间的关系式,使模型可自动计算出应有的外型,减少尺寸逐一修改的繁琐费时,并减少错误发生。
运用SolidWorks中的各项工具,能够快捷地对铸件进行厚度分析、起模分析、结构分析等,检查铸件结构设计的合理性,避免传统二维平面设计中难以发现的壁厚设计不当,干涉等问题。铸造工艺方案确定后,借助其中的分型面、切削分割、型腔、组合、起模等特征,很快就可以得到外模、芯盒的计算机三维造型。利用质量特性工具,可以检查砂芯能否平稳地放置,将各砂型、砂芯装配起来,能够模拟下芯操作。在设计系列零件时,优势非常明显,做好一个基础模型后,建立系列零件表,输人各系列的尺寸,能够在几个系列中快速切换,避免重复性的工作。从模型能够直接生成工程图,指导模型的制造、零件的生产。本文附图中的三维模型,全部是在SolidWorks中完成的。
浇注系统开设得正确与否,对铸件的质量影响很大。浇注系统的设计,要根据具体的情况,正确选择类型和开设的位置,对各种可能方案进行反复比较,还要确定各组元的合理尺寸及其之间的比例关系,某一方面的失误都将带来不良的结果。选取Excel进行数据分析和计算,过程透明,操作简单,掌握一定基础知识的初学者就可以自已编制出适合于自己应用的程序。我们按常用的浇注系统计算公式编制了简易的程序,并将大量的成功例子输人进行分析验证,调整各经验值的大小,只要给出铸件的重量、外形等各尺寸,计算机就能够快速地制订出较合理的浇注系统方案,按此方法计算出来的浇注系统,经过实践的验证,铸件出品率较高,证明浇注系统设计合理。本文将以实例对以上方面进行详细说明。
1、起模分析
1.1用途
起模分析对于铸造工艺方案的制订有很大的帮助。
(l)可以使用起模分析工具来检查起模正确应用到铸件面上的情况。
(2)有了起模分析,可核实起模斜度,检查面内的角度变更。
(3)可利用起模分析找出铸件的分型线、浇注面和出坯面。
(4)应用起模分析后,可看出外模需设活块的位置。
(5)对芯盒的三维造型进行起模分析,能轻松设置芯盒的分边分块。
1.2实例
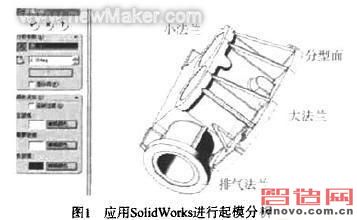
图1为对我公司某型号压缩机上的排气端座进行起模分析的情况。图中深色处为负起模区,即妨碍起模的位置。由图可知,小法兰、排气法兰下半部为负起模区,由图可初步制订出这样的方案,三箱造型,考虑到大法兰精度要求高,且为好放置排气口砂芯(图中仅看得见排气法兰处孔),大面向下,由大面起模,外模上小法兰(连同凸台)脱活块,排气法兰的下半部形状靠加一砂芯形成。
1.3操作方法
(1)打开模型,然后单击工具起模分析。
(2)在分析参数下,执行如下操作。
选择一平面、一线性边线或轴来表示起模方向。图1中选择的面为大法兰面,则系统给出的起模方向为垂直于此面的方向,图中小箭头所指为起模方向(意义参考图2)。要更改起模方向,可单击反转方向,也可使用图形区域中的小箭头来反转方向。输入参考起模角度,系统会将该参考角度与模型中现有的角度进行比较。
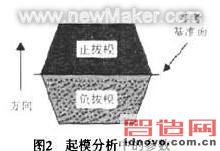

以上两参数选好后,点击计算,在图形区域将会根据设定的颜色显示出各种面来。"正起模"指面的角度相对于起模方向大于参考角度;"负起模"指面的角度相对于起模方向小于负参考角度;"需要起模"显示需要校正的面,这些面的角度大于负参考角度但小于正参考角度;"跨立面"显示包含正以及负起模类型的面,通常.这些为需要生成分割线的面。一般将负起模面设置成醒目的红色,以便发现。
将指针移动到模型上的任一区域,屏幕上将会动态显示该区域的起模角度的数值。
2 方案设计
2.1 用途
可通过分型面、切削分割、型腔、组合、起模等多种方式,将铸件的三维造型变换得到外模、砂芯、芯盒等的三维实体造型,进而检查外模起模是否顺利,芯盒设计是否合理;通过装配,可模拟下芯的情景,以发现可能出现的问题。以上操作,能检查工艺方案的合理性,若发现问题,可及时修正调整。也可设计好不同方案后,将各情况模拟出来,比较优劣,以得到最佳方案。
2.2操作方法
SolidWorks中有一系列的铸模工具。图3中的各工具的功能依次为:比例缩放,用于按指定的因子缩放模型;分型线,用于建立分型线以将核心和型腔分离;关闭曲面,用于查找并生成模具关闭面;分型面,用于在核心和型腔面之间生成分型面;切削分割,用于切削分割特征;型腔,用于插人一个型腔到基体零件中;起模,使用中性面或分型线按所指定的角度削尖模型面;分割线,将草图投影到弯曲面或平面,从而生成多个单独面;等距曲面,使用一个或多个相邻的面来生成等距的曲面;直纹曲面,从边线插人直纹曲面;延展曲面,从一条平行于一基准面的边线开始来延展曲面;平面区域,使用草图或一组边线来生成平面区域;缝合曲面,将两个或多个相邻、不相交的曲面组合在一起;起模分析,根据模具起模方向分析面的起模角度;底切检查,识别形成底切的面。
另外,利用SolidWorks动态修改尺寸这一功能,可快捷地实现加工面"加工余量"、砂芯留"间隙"的操作。常用的还有"组合"这一工具,通过多个实体的加、减、并逻辑操作,可将铸件模型转换成砂芯、外模、芯盒等三维造型。还有"分割"工具,可将一个实体用曲面或平面分割成多个实体,可用于模拟芯盒分边,外模脱活块等。
2.3 实例
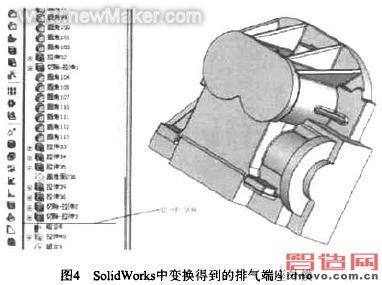
上文中的图1为我公司某型号压缩机的排气端座的三维造型的一部分,排气法兰的下半部形状为一砂芯形成,我们通过将一拉伸特征与铸件模型进行逻辑加的操作,就从上述模型变换到了如下的铸件外模三维造型(见图4)。这时候可再次使用起模分析,检查是否有妨碍起模的地方。如果将拉伸特征与铸件模型进行逻辑减操作,则可得到砂芯的三维造型。
SolidWorks中的退回控制棒,随时可通过拖动来将模型退回到中间过程(例如退回到为铸件状态时〕,观看铸件局部的细节,也可很快地拖回到现状态,通过比较看工艺方案设计得是否合理。
3砂芯设计
3.1用途
(1)检查砂芯的重心所在,看砂芯是否能够平稳放置。
(2)对芯盒分块,便于顺利出砂。
(3)检查下芯时各砂芯砂型间是否有妨碍。
3.2操作方法
砂芯的生成,一般是在铸件的基础上,通过分割、组合、动态修改尺寸(加余量、留砂芯间隙)、起模分析等操作,再加上芯头,加缩放比例,起模斜度,变换成各砂芯的三维造型。类似的操作,可将之转换成芯盒的三维造型,通过分型面对芯盒分割,进行起模分析,可检查芯盒分边是否合理,能否顺利地出砂。
检查砂芯的重心,要对砂芯应用到质量特性,其中可看出砂芯重心所在,垂直于砂芯底面观察,即可看出砂芯的重心是否落在底部芯头范围内,知道它是否能够放置平衡。
检查下芯时是否有妨碍,需要用到装配的概念。
3.3实例
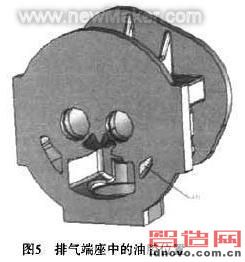
图5为我公司某型号的排气端座,图面朝向的大面为排气面,其所对的背面接增速箱,因设计条件的限制,排气温度较高,为降低机器运行时温度,不致影响使用性能,机体、排气端座、吸气端座上均开设有油腔,油在其中循环,以带走热量.为了使散热良好,面积应尽量大,流动阻力尽量减小,为此综合多方面的考虑设计了如图的两个油腔。左右的油腔均由砂芯形成,但右边的油腔制造起来时有不少困难,首先,它在两个端面上的形状变化较大,因油腔与一进油孔相连,又要求它离小法兰面一定的距离内形状不能变化,否则无法与油孔相连。我们用放样这一特征按上述要求做出了砂芯的模型,设置为不与基体合并,再通过逻辑减在基体上减去,这样便生成了铸件的模型,通过退回控制棒,可随时退回到砂芯的状态。下面我们通过质量特性来检查此砂芯是否能放置平稳,图6中深色的区域为砂芯的底面,如果整个砂芯的重心落在深色区域,则砂芯可平稳放置;反之,则下芯后无支撑时砂芯将会倾斜。考虑到此处结构紧凑,靠近转子孔这一重要位置,原则上不使用芯撑,以免对局部造成不良影响。我们将采取措施对砂芯本身进行处理,以求在满足要求的前提下达到放置平稳的目的。
放样就是通过在轮廓之间进行过渡生成特征。未调整前的砂芯就是通过放样特征形成的。为了达到在离小面一定距离不变形的要求.在离小面一定距离的平面上插入了一个与小面形状一致的面,让大面、小面、插人面上的截面均作为放样截面。现在为将重心平衡过来,在离大端面一定距离的平面上再次插人一放样截面,添加到现有放样,即让大面形状在一定距离内也保持不变,现在再次对调整后的砂芯应用质量特性,我们看到,已初步起效,重心移到了深色的底部支撑区域内了,如图7所示。当然,图中的效果还不是很理想,还需继续对此砂芯进行细调,可以将大面保持的距离再增大一些,或将靠大面的平面上的截面形状向右下移动,以作进一步的平衡,达到较佳的受力情况。理论上分析后,在模型制作时做了严格要求,此铸件已完成,效果良好。
4壁厚检查
4.1 概述
为保证铸件的强度和避免出现冷隔和浇不足等缺陷,并防止过薄处的白口倾向,铸件应有适当的壁厚。铸件最小允许厚度与合金的成分及其流动性关系密切,也与浇注温度、铸件尺寸大小和铸型的冷却能力及其它热物理性能有关。但是铸件的壁厚也不是越厚越好,砂型铸件具有双面结晶这一特点,过厚处易出现收缩类缺陷(缩松等),过厚的铸件,其重量、体积也随之增加,经济性不好。厚度分析实用程序决定零件中不同的厚度值。它识别薄区和厚区,并确定零件中与指定目标厚度相等的部分。壁的相互连接处往往会形成热节,易出现收缩类缺陷。所以铸件的壁厚还应尽可能一致以达到比较均匀的冷却,使壁厚发生变化的地方逐渐过渡。为此,特别是对于新设计的铸件,希望能在铸件设计阶段即能比较清晰准确地检查铸件各处的壁厚,尽量做到各处壁厚均匀,无过厚或过薄现象出现。但是在传统的二维平面工程图中,很难去判断一个复杂铸件的壁厚是否设计的合理。这一问题,甚至在模样制作阶段也很难发现,但是到了铸件的生产阶段,这一问题即会暴露出来,但这时,要重新去改设计图纸,改模样,重新铸造,浪费了人力物力,且在任务紧急时会耽误宝贵的时间。我公司曾经出现过这样一个问题,某型号的新产品在设计时,机体因内外壁均是复杂的曲面,二维工程图无人能检查出问题,模样制造时,外形由外模形成,内部形状由砂芯形成,当时也没有发现问题,但在合箱的时候,就发现某处的壁厚过薄,铁液流不过去,这样的铸件自然成了废品。但应用SolidWorks,就不会有类似的问题发生,可避免不必要的损失。另外,也可将零件进行厚度分析,以确定铸件上需加的余量(详见下例的说明)。
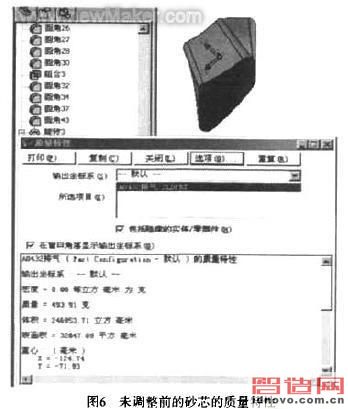
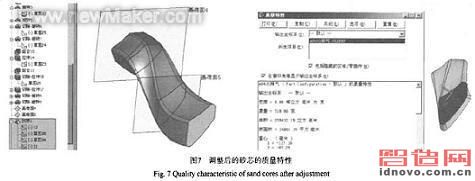
SolidWorks Utilities中的厚度分析可分析零件中不同的厚度值,识别薄区和厚区,并确定零件中与指定目标厚度相等的部分。进行薄区识别时,输入分析参数,即符合强度、刚度条件、工艺要求的最小壁厚,系统将显示小于最小壁厚的警戒值,通过不同颜色区分,一目了然。进行厚区识别时,输人最小壁厚值作分析参数,再输人一个认为过厚的壁厚,系统将以不同颜色显示各厚度范围,可从中看出热节区的分布(一般是较醒目的红色区域),壁厚是否均匀(均匀的壁厚各处的颜色基本是一致的)。
4.2实例
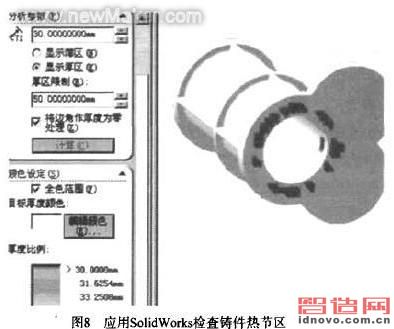
我公司某型号的油活塞缸体在试压时,经常在大法兰与筋板交接处出现泄漏现象,为此我们将此铸件的模型进行了厚度分析,可明显地看出(如图8),此处壁厚较大(图中深色的区域),且为相互连接处,热节区容易出现疏松等缺陷,从而导致此处经常会泄漏。在理论上作了分析后,从浇注工艺上采取了对应的措施,问题有所好转。在新型号产品设计时,针对此种结构的油活塞缸体此处形成热节的情况,对结构作了调整,将大法兰与缸体分成了两个零件,经同样的壁厚分析,壁厚分布较均匀,工艺性好,从而避免了此类问题的发生。
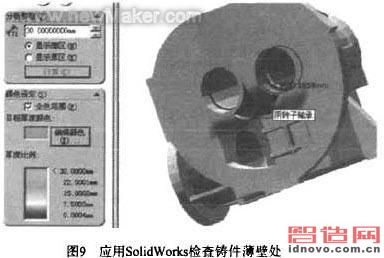
图9为我公司某型号的排气端座,使用SolidWorks来检查零件薄壁处,结果发现阴转子轴承孔与排气孔口相连处壁厚过薄(图9正中较深色的区域),将指针移上时,显示指示位置处的壁厚及特征名称,结果发现此处的壁厚仅有7.66 mm,显然对于这个铸件来说是太薄了,但设计时限于转子孔的位置和排气孔口均不能更改,且此壁厚经计算满足了强度条件,为此,设计铸件工艺时,我们特意将转子轴承孔的余量取得较大,以使铸件的壁厚不致太薄,多加的余量在粗加工时很方便就可去除。应用同样的方法,我们制作了曾出现壁厚过薄的某型号的机体更正前后的对比模样,发现问题很明显,如果当时能够早一步在计算机中作出类似的分析,则不会出现模样返工的现象。
5浇注系统计算
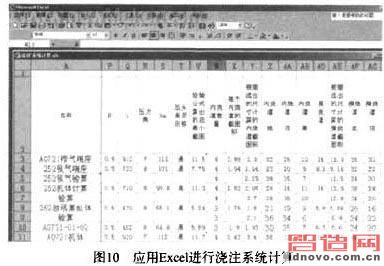
我公司的铸件中有相当一部分是系列化的,即不同的型号之间除了尺寸大小方面的差别外,形状方面的差别很小。我公司I, II型压缩机经过几十年的试验改进,已经形成了一套成熟的模样制造、零件加工的工艺,在这种情况下,如果在旧型号的基础上设计一新型号的铸件,为铸件设计浇注系统时,就可以应用到Excel的功能,先选取常用的伯努利方程、奥赞公式等,将大量的成功例子输人,通过对平均静压头、浇注时间、直、横、内浇道之间的比例关系等进行分析验证,并将各经验表格输人,经过调整各经验位的大小,最后综合.得到符合我公司情况的公式,如图10,在图示的第3行中输人公式,通过填充句柄拖动,公式在下面的每一行中都以同样的规律得以体现,然后将重量、壁厚等需输人的条件的单元格锁定取消,最后锁定整个工作表,因为系统默认的单元格为锁定,这样除了可以在设计条件栏输人以外,其他单元格均被锁定,可以防止误操作造成原始数据的改动,保护了程序的稳定性。就这样编制了简易的适合我公司铸件浇注系统计算的小程序,只要在相应位置输人铸件的重量、外形等各尺寸,计算机就能够快速参照成功例子制订出较合理的浇注系统方案。按上述方法快速计算出的浇注系统,十余个新产品通过试制,非常成功。
6重量计算
6.1概述
重量在零件设计时,有时是一项重要的参数。传统的二维平面工程图,通常是这样计算重量的,就是将零件折分成为多个简单的几何体,分别计算,再将之加减乘除,从而得出近似的重量,但对于铸件来说,特别是复杂的铸件,外形内腔为曲面变化,用这种方法很难得到准确重量的。因而特别是在很多需要标注重量的场合,设计者一般是先估算出一个误差较大的重量,等零件制作出来后,再称取重量,对设计图纸作调整。通过SolidWorks,只要有几组试验数据提供,从中得到此种材料(如HT200)的密度,就可很快地利用质量特性得到零件的重量。
在我公司一大型新产品的设计中,需要估算整个压缩机的重量,检查加工、装配时行车、装配工作台等是否能够承受重量,以决定是否需要对车间进行改造。端盖、隔圈等简单规则件很容易计算重量,但排气端座、机体、吸气端座等复杂铸件很难以通常的方法来估算重量,对这些复杂铸件在计算机中均作了相应的三维造型,作质量特性的计算,其总重量大约为3. 5t,现有的3t行车无法满足要求,为此购买了新的5t行车。
6.2实例
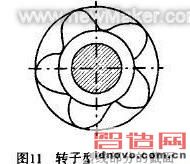
我公司的球铁转子,在零件加工完毕后要进行动平衡试验,选取的动平衡试验等级为G2.5级,确定动平衡试验等级后,实际操作时需用到的许用不平衡力矩是这样计算的:许用不平衡力矩=允许偏心距*重量/2,设计时,必须要知道转子的重量,才能制订出合理的技术条件。但是我公司转子的型线部分是由外单位计算出的曲线,我公司仅仅知道曲线上各点的坐标值,且此曲线通常是较复杂的曲线(图11),无法用简单的圆弧去模拟。
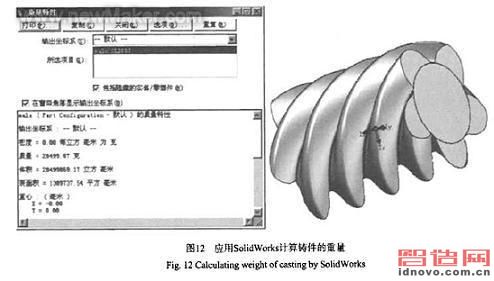
为此我们在SolidWorks中对之进行了重量计算。首先使用样条曲线将各点拟合成光滑曲线,通过以螺旋线为曲径扫描,生成了转子部分的形状,转子两头轴颈形状非常简单,图12中未表现出来。在质量特性的选项中将同牌号材料的经验密度输入,就可得到下图中的数据,很快就知道转子螺旋部分的重量。再加上其它部分的重量,经过上面公式,则可得到试验所需的许用不平衡力矩。
7结束语
将计算机引人到铸件的结构设计和工艺编制中,能提高效率,节省时间,避免错误。但计算机毕竟只是工具,它是按照人的思路来工作的,更多的应用还有待大家去发掘。
相关文章
- 2021-09-08BIM技术丛书Revit软件应用系列Autodesk Revit族详解 [
- 2021-09-08全国专业技术人员计算机应用能力考试用书 AutoCAD2004
- 2021-09-08EXCEL在工作中的应用 制表、数据处理及宏应用PDF下载
- 2021-08-30从零开始AutoCAD 2014中文版机械制图基础培训教程 [李
- 2021-08-30从零开始AutoCAD 2014中文版建筑制图基础培训教程 [朱
- 2021-08-30电气CAD实例教程AutoCAD 2010中文版 [左昉 等编著] 20
- 2021-08-30电影风暴2:Maya影像实拍与三维合成攻略PDF下载
- 2021-08-30高等院校艺术设计案例教程中文版AutoCAD 建筑设计案例
- 2021-08-29环境艺术制图AutoCAD [徐幼光 编著] 2013年PDF下载
- 2021-08-29机械AutoCAD 项目教程 第3版 [缪希伟 主编] 2012年PDF