1.砂轮的传统加工方法有哪些缺点?
砂轮经过焙烧和固化等工序后,其尺寸、形状和各表面相互位置精度,均达不到使用的技术要求,必须经过车削、研搓和磨削。使用砂轮的单位也因生产急需和砂轮的规格与使用要求不符,也须车削。由于客观技术原因,国内外大都采用传统的刀碗来车削。在用它加工的过程中,砂轮以较高的线速度(300~400m/min)带动淬火的45号钢薄壁刀碗旋转,并进行走刀,将砂轮的多余量去除。由于被加工的砂轮与刀碗高速旋转,造成加工中的粉尘和噪声很大,切削深度和进给量很小,故加工效率低和综合成本高,操作者劳动强度大。如采用大颗粒金刚石刀具,价格昂贵,而且由于金刚石的抗弯强度低,切削中易损坏,造成用它切削砂轮时的切削深度和进给量很小,一般只在精加工时采用。
2.采用人造聚晶金刚石复合片刀具切削砂轮有哪些特点?
人造聚晶金刚石复合片(PCD),是20世纪70年代研制成的一种超硬刀具材料。用它制成的刀具,被用来切削各种有色金属和非金属,而且可以用来切削砂轮。在用它切削砂轮时,有以下特点:
(1)有很高的硬度和耐磨性:聚晶金刚石层的硬度一般在HV7000~9000,而且各方向一致,是一般砂轮磨料硬度的2~4倍。用它切削砂轮的耐用度很高,其体积磨耗比可达1/1300万。
(2)有很高的抗弯强度:金刚石的抗弯强度为210~490MPa,而PCD刀片的聚晶层下面有较厚的抗弯强度较高的硬质合金支承,其复合抗弯强度可达1500 MPa,所以在切削过程中,不产生崩刃或断裂。
(3)砂轮在切入切出时易崩边:用较大主偏角的刀具切削砂轮时,切入切出处易崩边。为了解决这一问题,采用圆形刀片,改变了主偏角,使切入切出平稳。在进给量为1~1.5mm的情况下,未发生崩边现象。
(4)切屑呈粉末状:切削砂轮的切屑呈粉末状,刀具磨损的形式是后刀面磨损,主要承受砂轮磨料的磨损。
(5)切削力和切削温度较低:金刚石有高的导热系数,为硬质合金的1.5~9倍,为铜的2~6倍,使切削区的温度很快传出。因此,用PCD刀具切削树脂结合剂或陶瓷结合剂砂轮的温度,比切削金属低许多倍。
3.怎样用PCD刀具切削砂轮?
用PCD刀具来切削硬度达HV2000~4000的砂轮,如同用刀切豆腐一样容易,这说明PCD刀具用来切削砂轮比较合适。
(1)刀具:利用PCD刀片制作成如图15-1和图15-2所示的机械夹固车刀,用来车外圆、内孔和端面。它的纵向和横向前角为-10°,后角为10°。一律采用圆形刀片,使切入切出平稳,砂轮不崩边。
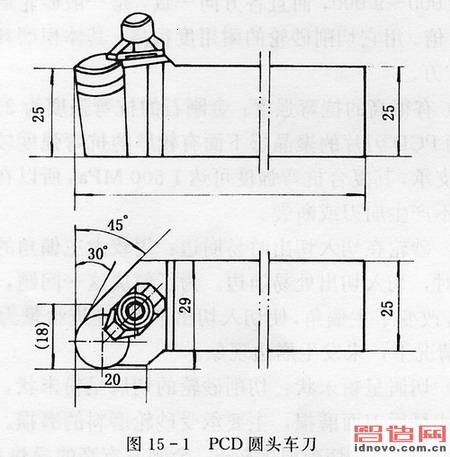
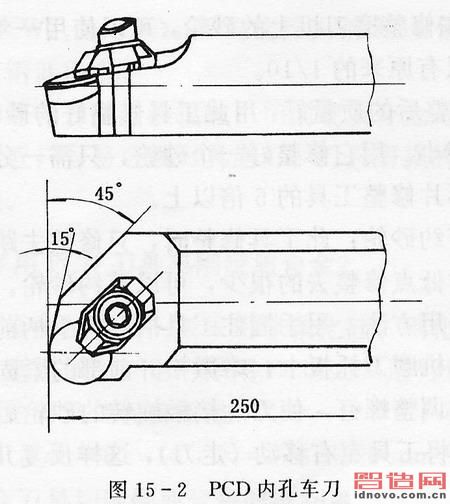
(2)切削用量:通过实践,PCD刀具车削砂轮的切削用量,一般采用νc= 25~40m/min,ap=4~5mm,f=1~1.5mm/r。
(3)除尘:用刀具车削砂轮时的粉尘不可避免。用PCD刀具切削砂轮时的粉尘,远远低于传统的刀碗挤压。为了防止粉尘飞扬,可以采用喷水雾的办法。
在20世纪80年代初,开始用PCD刀具车削砂轮,采用上述的刀具与切削用量,就成功地车完了内孔小于150mm、厚度120mm的50片砂轮。这时的PCD刀头一边磨损不到0.5mm,反映出这种刀具用来切削砂轮的耐用度很高。
4.用人造聚晶金刚石复合刀片修整砂轮有哪些特点?
将人造聚晶金刚石复合刀片(PCD)做成如图15-3所示的工具,用来修整磨刀机上的砂轮,显示出比其他修整工具突出的特点。
(1)刀片耐磨使用寿命长:由于PCD刀片硬度很高,耐磨性非常好,用它来代替传统的齿形片砂轮修整工具和金刚石笔来修整砂轮,一般的情况下,一个机加工车间用一个PCD刀片来修整磨刀机上的砂轮,可以使用一年以上,而修整的成本只有原来的1/10。
(2)修整后的质量好:用此工具修整好的砂轮十分平整,径向跳动很小。用它修整好一个砂轮,只需一分钟左右,其效率是齿形片修整工具的5倍以上。
(3)节约砂轮:此工具修整时,只修整去跳动和不平处的高点,对低点修整去的很少,可以节约砂轮。
(4)使用方法:用手握住工具柄,将手柄前端的定位平面靠在砂轮机磨刀托板上,略微松开前部的紧固螺钉,用手旋转后部的调整螺钉,使刀片接触旋转的砂轮后,再视情况吃刀,然后将工具左右移动(走刀),这样反复几次后,即将砂轮修好。
5.硬质合金有哪些切削特点?
硬质合金在人们头脑里的概念是它非常硬而脆,用来作刀具材料、模具等耐磨零件,加工它的方法,只能采用磨削。由于超硬刀具的出现,硬质合金也可用刀具来切削,其特点如下:
(1)硬度高、脆性大:硬质合金的硬度为HRA85~92.5(HRC67~81),比一般淬火钢的硬度高出HRC20,所以切削时极为困难。它没有塑性,而且脆性很大,受切削力和刀具的挤压,切入切出处极易崩边。
(2)切屑呈粉末状:由于硬质合金脆性很大,所以切屑全呈粉末状,根本不产生积屑瘤,已加工表面粗糙度容易达到。
(3)导热系数较高,切削温度较低:硬质合金的导热系数为17~88 W/(m·K),平均比淬火钢高15倍,所以切削温度比淬火钢低得多。
(4)切屑与刀面接触很短:切削硬质合金时,切削力集中在刃口附近,容易造成刀具崩刃。刀具磨损的主要形式是后刀面磨损。
6.怎样用PCD刀具车削硬质合金?
硬质合金的加工,一般采用绿碳化硅、碳化硼砂轮和金刚石磨轮来磨削加工,也可采用PCD刀具进行切削加工。
切削时的刀具几何参数是:γo=-5°~0°,αo=8°~10°,kr=30°~45°,k′r=8°~10°,rε=0.8~1.5mm。
用PCD刀具切削硬质合金时的切削用量是:νc=25~35m/min,ap=0.1~0.5mm,f=0.1~0.15mm/r。切削YG15或YG20时取大值。
切削时为了防止因硬质合金脆性大而崩边,在切入切出处要适当减小进给量或先在此处倒一个角,并要使刀刃锋利。在切削过程中,可选煤油作切削液。
7.用PCD刀具加工模具用硬质合金有哪些优越性?
(1) 改善冲模的强度特性和使用性能:用PCD刀具切削钨钴类(YG15、YG20)硬质合金冲模时,加工表面产生较大的残余压应力,可改善模具的强度特性和使用性能。如用绿碳化硅砂轮磨削,磨削时产生的高温,使工件表面产生退火层、微裂纹和残余拉应力,影响磨具的使用性能。
(2)提高加工效率:如用美国通用公司生产的PCD刀具,它的纵、横向前角均为-5°,后角为5°,车削硬度为HV1204的钨钴硬质合金,在νc=28~56m/min、ap=0.5mm、f=0.25~0.35mm/r、采用乳化液的情况下,金属切除量为3.5~8cm³/min,其切削效率高于现在使用的其他加工方法。
(3)有较高的刀具耐用度:用日本住友电器公司生产的DA200、DA150和DA100的PCD刀片车削YG15硬质合金,在νc=15 m/min、ap=0.5mm、f=0.1mm/r的情况下,用DA100这种粗晶粒和细晶粒混合组织的刀片,耐用度为30min,后刀面只磨损了0.2mm。
8.用CBN刀具切削硬质合金的实例有哪些?
采用CBN刀具切削硬质合金(YG15、YG20、YG25),可以代替电物理加工、金刚石刀具切削和金刚石磨轮磨削。
(1)镗孔:在硬质合金衬套上镗孔,精度为IT6~IT8,表面粗糙度Ra为1.6~0.8μm。切削用量是:νc=15m/min,ap=0.2~0.5mm,f=0.1~0.15mm/r。刀具几何参数是:γo=-5°,αo=6°~8°,κr=45°,κ′r=15°,rε=0.5mm。用CBN刀具镗孔的效率比用金刚石磨轮磨削高10倍左右。
(2)车外圆:用CBN刀具在φ40mm、长100mm的硬质合金冲头上,切去3.5 mm余量,只需25min,如用金刚石磨轮磨削,则需要215min。
(3)断续车削:CBN刀具不仅可以连续车削硬质合金,而且可以进行断续车削。如断续车削YG20、YG25的硬质合金套筒时,νc=30m/min,ap=0.35mm,f=0.034mm/r。刀具的几何参数是:γo=-6°,αo=8°,κr=45°,刀具的耐用度为6.5min。
用PCD和CBN刀具切削加工精度特别高的零件是困难的,还是要用金刚石磨轮磨削。这是因为切削硬质合金时的径向分力FP 很大,导致刀具发生退让。当νc=10m/min、ap=0.5mm、f=0.1mm/r、后刀面磨损0.05mm时,FP为400N左右;VB=0.1mm时,FP=700N;VB=0.2mm时,FP=1300 N。因此,用超硬刀具切削硬质合金,必须选用工艺系统刚性好的工艺条件,而且也只能加工精度为IT6左右、粗糙度大于0.8μm的零件。
9.怎样对磁钢进行磨削?
磁钢是磁合金的总称,是现代最重要的永磁材料。它具有良好的磁性,在机电工业中得到广泛的应用。常用的磁钢有Al—Ni—C05和Al—Ni—C08两种,通称为五类磁钢和八类磁钢。
(1) 磁钢的磨削特点:它具有硬脆的性能,在磨削过程中易产生碎裂、烧伤和崩边等现象,特别是在砂轮行出工件时最易产生。五类磁钢比八类磁钢的加工性稍好一些,而八类磁钢的磨加工性就十分困难。八类磁钢的晶格有明显的方向性和定向导热性,在磨削过程中所产生的缺陷与结晶方向有密切关系。当磨削方向与柱状结晶组织方向一致时,磁钢平面的锐边,几乎不产生崩边现象,即使有也相当小。当磨削方向与柱状结晶组织方向相垂直时,在砂轮出口处就会崩边,严重时会造成片状剥落。所以磨削磁钢与磨削其他材料不一样,磨削时必须注意。
(2)磁钢的磨削:应选用绿色碳化硅或氧化铝为磨料,粒度为46号~60号,硬度为软2和中软1的大气孔砂轮。另外,还可以采用在碳化硅砂轮开槽的间断磨削(参考本书基础知识第72和73题)。在磨削时应采用微量进给,加大冷却液冲洗。为了防止在砂轮行出时工件崩边,可在工件两端接合两块普通钢的防护板,如图15-4所示。在磨削过程中,必须保持砂轮锋利,使砂轮与工件接触时发出“ 沙沙”的声音。当砂轮与工件接触时发出“嗡”声时,就必须修整砂轮,否则会因砂轮变钝,而产生烧伤等缺陷。砂轮大于工件覆盖面时,必须加大冷却液的冲洗,加速散热,并减少工件的进给量,防止砂轮对工件的瞬间冲击以提高了工件表面质量。
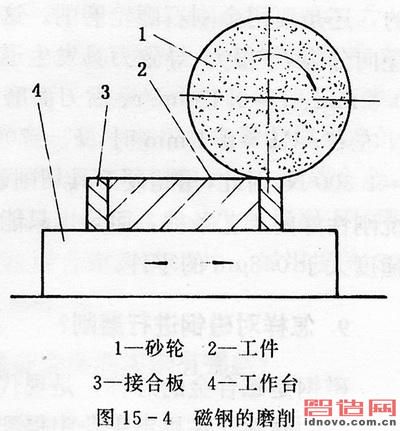
相关文章
- 2021-09-08BIM技术丛书Revit软件应用系列Autodesk Revit族详解 [
- 2021-09-08全国专业技术人员计算机应用能力考试用书 AutoCAD2004
- 2021-09-08EXCEL在工作中的应用 制表、数据处理及宏应用PDF下载
- 2021-08-30从零开始AutoCAD 2014中文版机械制图基础培训教程 [李
- 2021-08-30从零开始AutoCAD 2014中文版建筑制图基础培训教程 [朱
- 2021-08-30电气CAD实例教程AutoCAD 2010中文版 [左昉 等编著] 20
- 2021-08-30电影风暴2:Maya影像实拍与三维合成攻略PDF下载
- 2021-08-30高等院校艺术设计案例教程中文版AutoCAD 建筑设计案例
- 2021-08-29环境艺术制图AutoCAD [徐幼光 编著] 2013年PDF下载
- 2021-08-29机械AutoCAD 项目教程 第3版 [缪希伟 主编] 2012年PDF