本文以AutoCAD2006为平台,VC++.NET为开发环境,结合AUTODESK公司推出的Object—ARX2006二次开发工具,根据中国第二重型机械集团铸造分厂的大型铸钢件铸造工艺要求,采用参数化设计的方法,进行针对大型铸钢件的铸造工艺CAD系统的开发。此工艺CAD系统在实际运用中,改变了
人工纸板绘制工艺和手工查阅铸造手册的状况,加快了新产品的开发速度,提高了其市场竞争力。工艺人员通过计算机辅助设计绘图,并运用此工艺CAD系统进行铸造工艺设计,减轻了劳动强度,提高了工艺设计效率。
1 大型铸钢件铸造工艺CAD系统的设计
大型铸钢件铸造工艺CAD系统是一个基于AutoCAD的二次开发系统,对大型铸钢件的铸造工艺CAD系统应施行模块化设计。首先,要规划好系统的结构。本文把铸造工艺CAD系统大致上分为六大模块:浇注系统、冒口系统、冷铁系统、砂芯系统、辅助系统、工艺参数系统。整个系统的结构如图1。每个系统模块完成所对应的大型铸钢件铸造工艺过程,整个铸造工艺CAD系统涵盖大型铸钢件铸造工艺设计的全部流程。
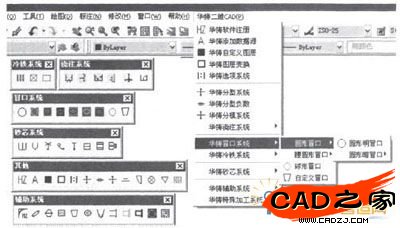
图1 铸造工艺CAD系统结构图
2 开发工具与开发环境
一个CAD系统所支持的各种程序设计语言统称语言开发环境。语言开发环境是CAD系统开放式结构的一个重要组成部分,它可以将高级语言的运算、判断及字符处理功能和CAD系统的图形处理功能有机地结合起来,从而为CAD系统的二次开发提供强大的工具。
基于AutoCAD2006平台,以ObjectARX2006为开发工具,开发环境为VC ++. NET2002。Object-ARX的最大特点是引入了面向对象的编程思想,提供了大量的类库,而且ObjectARX生成的是动态链接库,共享程序地址空间,相比之前通过IPC(进程间通信)进行交互, Obj ectARX开发的系统效率更高,有更好的控制能力。ObjectARX支持与Microsoft的基础类库(MFC)的混合编程,使得开发者能够创建基于MFC的用户界面,其外观和内建与AutoCAD的用户界面完全相同,与其它应用程序如ADS和Lisp相比,ObjectARX充分利用了Windows的现有资源,可以方便、高效和可靠地设计出具有典型Windows风格的AutoCAD应用程序。
3 系统的开发与实现
大型铸钢件铸造工艺CAD系统的二次开发过程中,冒口系统、冷铁系统、砂芯系统及辅助系统中的吊把和铁芯头、铁芯座、都采用参数化设计方法进行设计。参数化设计方法就是指在保持图形结构的拓扑关系不变的情况下,通过设置相应的参数来控制图形的几何尺寸大小,部分参数值的改变可以导致设计图形的自动修改。这种设计方式显著地改善了图形设计的重构能力和设计柔性。
3.1 大型铸钢件窗口系统设计
普通铸钢件的冒口尺寸设计一般采用普通模数法计算,取冒口模数Mr=(1.1~1.2)Mc(铸件模数),并由补缩效率η=14%~20%来验证。为了确保大型铸钢件的质量,Mr往往要取上限,但这样可能会造成相当大的浪费。故在二次开发中对于大型铸钢件采用动态模数法:在冒口一铸件凝固体系中,冒口不断地向铸件补缩,使得Mr和Mc处于动态变化状态。当铸件凝固结束时,铸件的实际体积增加到Vc+εVc,冒口的残余体积减少到Vc-εVc。因此,这时它们的确切模数分别为:
从理论上讲,当
时,冒口与铸件凝固时间相等,而在凝固结束以前Mr均大于Mc,铸件可得到充分补缩。按此原则制定冒口尺寸是最经济、合理的。
大型铸钢件多为单批或小批生产,且制作冒口需花费大量的木材和工时。所以二重铸造厂将冒口尺寸进行标准化和系列化,这样就可以充分的发挥冒口模型的使用价值,节省大量的人力,物力。在用铸造工艺CAD系统绘制冒口时,我们根据大型铸钢件的结构和工艺流程,确定冒口的尺寸和类型,点击所需类型的冒口图标,以圆形明冒口为例,在编辑框中输入冒口的尺寸参数、视图类型及冒口线型,并根据需要计算出冒口重量和冒口模数。参数设置完毕后,点击“开始绘制冒口”按钮,进入冒口绘制阶段,此时,工艺人员用鼠标选取冒口放置平面及方向,系统自动生成冒口的3种视图,并自动标注尺寸。圆形明冒口设计界面如图2所示。
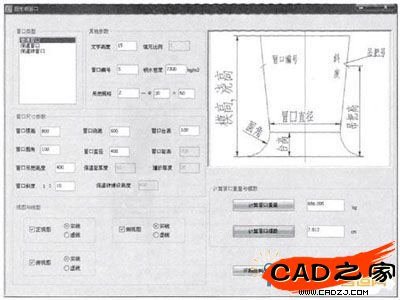
图2 圆形明冒口设计界面
3.2 大型铸钢件浇注系统设计
大型铸钢件几乎都是采用漏包浇注,设计步骤为:首先计算浇注时间和平均压力头,并运用流体力学公式计算阻流截面积,然后选择截面比计算各单元截面积,并结合浇道结构和截面参数设计各个浇道。
根据二重铸造厂大型铸钢件的铸造工艺要求,浇注系统分为3部分:单层浇注系统、多层浇注系统和冒口补浇多向浇注系统,其中每个部分又分为俯视和侧视两种视图方式。以单层浇注系统为例,首先计算出直浇道、横浇道和内浇道的截面尺寸和道数,然后在绘制俯视图时,鼠标点击各浇道的放置位置,程序自动生成各个浇道并进行标注。绘制侧视图时,在编辑框中输人浇道尺寸参数,点击“开始绘制”按钮,自动生成侧视图,再用鼠标点击确定放置位置。浇注系统单层侧视图设计界面如3所示。
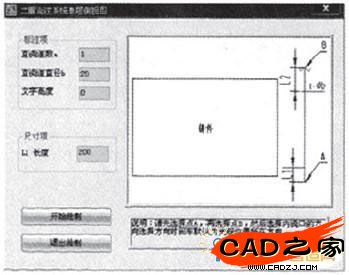
图3 浇注系统单层侧视图设计界面
3.3 大型铸钢件冷铁系统设计
大型铸钢件壁厚较大,凝固时的液态收缩与凝固收缩值也较大,单靠冒口往往不能充分补缩铸件,所以普遍使用冷铁。冷铁按在铸型中所处的位置可分为内外两种:外冷铁设置在砂型表面;内冷铁设置在相当铸件热节部位的型腔之中。在实际的冷铁设计中,应根据生产设计经验调整冷铁尺寸参数和布置方式,以更有效地满足工艺要求。
根据二重铸造厂大型铸钢件的铸造工艺要求,将冷铁系统分为规则外冷铁、不规则外冷铁和内冷铁3种。以规则外冷铁为例,先依据激冷区的铸钢件的结构,计算出所需的外冷铁的尺寸、块数和摆放位置,然后再在对话框中设置外冷铁尺寸参数、块数、线型和绘制方式。点击“开始绘制”按钮,用鼠标选取放置外冷铁的矩形区域,系统自动按要求完成外冷铁的绘制并自动标注。规则外冷铁设计界面如图4所示。
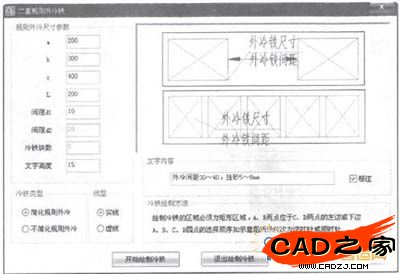
图4 规则外冷铁设计界面
3.4 大型铸钢件其他s艺CAD系统的设计
其他的一些常用的铸造工艺,如绘制分型线、分模线和分型负数等功能都包括在铸造工艺CAD系统中,工艺人员可以很方便地运用鼠标来指定位置,系统自动生成相应的工艺符号与参数。在工艺卡的绘制中,系统采用ODBC(开放数据库互连)技术,将工艺卡中的信息储存在数据库中,工艺人员依据不同铸钢件的工艺要求,方便地改写工艺卡,自由拖动技术能使工艺员拖动工艺卡放置在任何合适的位置上,工艺卡的设计界面如图5所示。以上功能的具体实现,限于篇幅,本文不再详述。
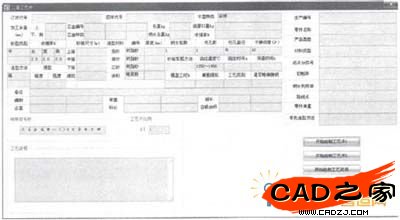
图5 工艺卡设计界面
4 应用实例
以二重铸造厂设计的上支撑轴承座为例。该铸钢件的最大外轮廓尺寸为1 266 mm X 610 mm X 1 172 mm,重3 252 kg,属于中等复杂程度的较大型铸钢件,且其铸造工艺较典型。设计步骤如下。
根据铸钢件结构特点和技术要求,确定浇注位置,利用浇注系统设计模块,计算出直浇道、横浇道和内浇道的直径,在主视图和侧视图上完成浇道的绘制。在轴承座长边侧面进行分型,绘制分型线并标出上下型。
通过特殊加工量与分型负数模块,确定工艺参数值,在铸件图上选择绘制位置,完成绘制,并将需铸死的位置绘制铸死符号。根据轴承座中空位置的尺寸大小确定砂芯的尺寸与间隙,并绘制砂芯引气和砂芯固定符号。根据铸钢件热节的大小和位置及最后凝固部位的体积和表面积,计算出铸钢件的模数,由此确定冒口的模数,然后根据铸造工艺要求选择圆形保温明冒口,选择冒口放置位置并完成绘制。在轴承座外壁较厚部位上放置外冷铁,然后将绘制好的铸造工艺图和工艺卡打印输出。工艺设计最终结果如图6所示。
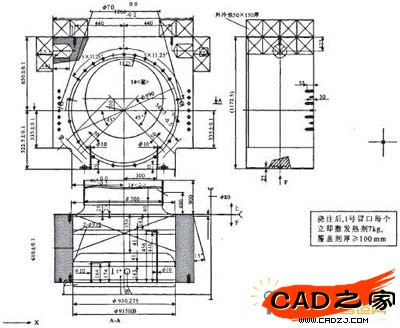
图6 上支撑轴承座铸造工艺图
5 结论
以AutoCAD2006为平台,VC++.NET2002和Object2006为二次开发工具,针对大型铸钢件的铸造工艺要求开发了铸造工艺CAD系统。此系统的功能包括了大型铸钢件铸造工艺设计的全部流程,并以工厂实际需要建立了冒口、铁芯头铁芯座和工艺卡等数据库。通过尺寸驱动方式,工艺人员经过简单的操作可快速准确地进行铸造工艺设计,减轻了其工作强度,提高了工作效率
相关文章
- 2021-09-08BIM技术丛书Revit软件应用系列Autodesk Revit族详解 [
- 2021-09-08全国专业技术人员计算机应用能力考试用书 AutoCAD2004
- 2021-09-08EXCEL在工作中的应用 制表、数据处理及宏应用PDF下载
- 2021-08-30从零开始AutoCAD 2014中文版机械制图基础培训教程 [李
- 2021-08-30从零开始AutoCAD 2014中文版建筑制图基础培训教程 [朱
- 2021-08-30电气CAD实例教程AutoCAD 2010中文版 [左昉 等编著] 20
- 2021-08-30电影风暴2:Maya影像实拍与三维合成攻略PDF下载
- 2021-08-30高等院校艺术设计案例教程中文版AutoCAD 建筑设计案例
- 2021-08-29环境艺术制图AutoCAD [徐幼光 编著] 2013年PDF下载
- 2021-08-29机械AutoCAD 项目教程 第3版 [缪希伟 主编] 2012年PDF