1 前言
目前,传统的航天器力学振动试验采用加速度响应控制方法,试验中的输入条件为真实数据的一条包络曲线。当试件发生共振时其有效质量降低加速度上升,当试件发生反共振时其有效质量上升加速度下降,因此无论是共振还是反共振其界面受力的变化并不大,共振和反共振一般都是伴随出现的,两者几乎处于同一频率。如果完全按照加速度包络曲线进行试验,反共振时的加速度下降就无法体现,在试件反共振时,振动台为了使试件达到共振时的加速度必然会大幅增加推力的输出,使试件受力严重过试验,导致损伤产品。如果为了通过试验会造成产品的过强度设计,这是导致航天器结构重量偏重的重要原因。目前通常采用共振点处加速度下凹控制来尽量避免过试验,但是这种方法缺乏理论基础,只能凭经验,在过试验和欠试验之间很难把握下凹的准确量。为了解决加速度控制的缺陷,航天发达国家提出了力限振动试验的设想。
力限振动试验是在加速度控制的同时限制界面力,当界面力达到规定量时控制加速度主动下凹,从而避免过实验。这是一种加速度控制与力的响应控制相结合的控制方式,可以有效解决纯加速度控制的缺陷。NASA与欧空局于上世纪末开始从事力限振动试验的研究,取得了大量成果,并在某些航天器的振动试验中进行了实践性的运用[1,2]。我国在近几年开展了一些力限控制方法的研究,在理论基础及实际应用中都取得了一定的成果[3]。
FMD(Force Measurement Device)是力限振动试验中的主要部件,它起到了传递和测量界面力的作用。文献[4]针对承力筒单向力限FMD进行了一系列分析,并给出了相关优化方法。文献[5]介绍了三向FMD测力环进行整星试验的结果。本文将针对某大型卫星进行三向力限FMD振动夹具设计,通过有限元分析算出各传感器的受力情况,选出最佳方案,最后分析说明大型三向FMD的设计要点及难点,并提出了相应解决办法。
2 力限FMD振动夹具设计
2.1 卫星相关参数说明
本FMD为了满足某大型卫星的力限振动试验而设计,该卫星质量2.7吨,质心高度1.65m。试验条件按三个方向最大加速度1g分别进行5~100Hz正弦扫频振动,在前期相同条件的纯加速度控制试验中,通过功放输出电流换算得垂直向最大推力为6.7吨,水平向最大推力为10吨,用于加速度控制的夹具质量为378Kg。
2.2传感器选型
该卫星力限振动试验以20吨振动台为激励源,由于要进行三向试验,且需要的测力范围较大,初步选择Kistler三向力传感器中量程最大的9377B和9378B为FMD的测力组件,见图1。
图1:9377B和9378B三向力传感器
这两种传感器外形和性能指标完全一样,不同点仅为导线接口位置相反。根据文献[4,5]的论述,为了保证FMD的刚度,对于大型FMD夹具应配置8个以上的传感器。在此选择9377B和9378B各4个,呈圆周均布,这样可使导线走向一致,有利于采集设备的安放。9377B和9378B具有测量范围大、灵敏度高、刚度高、抗干扰能力强等优点,在出厂前已进行了预紧和校准,客户只需将其安装在FMD夹具内即可使用。传感器安装方式极为简便,通过上下各4个M16螺钉进行紧固。其外形尺寸见图2,主要性能指标见表1。
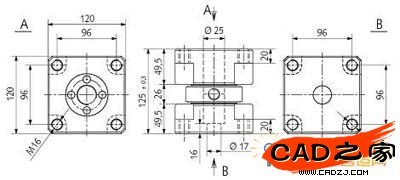
图2:传感器外形及安装尺寸
表1:传感器主要性能指标
2.3 FMD夹具设计
力限FMD夹具不同于传统的振动夹具,传统的振动夹具一般采用整体式结构,尽量避免螺接或焊接。力传感器测量的原理决定了其必须成为夹具中承力的主要部件,因此FMD夹具通常为分体式,通过螺钉连接为一个整体,在文献[5]中将FMD设计为一个测力环,然后其上再安装夹具。本设计将测力环与夹具进行整合使其具有测力和夹具的双重功能,该FMD夹具由三部分组成:上夹具、下夹具、力传感器,见图3。上夹具用于与卫星连接,下夹具用于与振动台连接。
图3:力限FMD夹具
为了使夹具在保证刚度的前提下重量尽可能轻,选用铸铝作为上下夹具的材料,并通过铸造成形。经计算上下两段夹具总质量为514.54Kg,传感器每个质量10.5Kg,共84Kg,整个FMD夹具总质量为598.54Kg,总高度295mm。本夹具由于采用的是组合连接方式,具有很高的灵活性,对于接口不同的卫星产品只需重新投产上夹具即可解决兼容性问题。8个力传感器的分布有两种选择,即正交分布和斜交分布。正交分布为在横向振动的X和Y轴上具有4个传感器,见图4。斜交分布为传感器与横向振动的X、Y轴具有22.5度的偏离,见图5。
图4:正交分布
图5:斜交分布
当做垂直向振动时,8个传感器在受力方向上处于同一平面,力由每个传感器均匀承担,正交与斜交对于传感器的受力几乎没有区别。当做水平向振动时,受力情况较为复杂,除了横向力外还具有倾覆力,且传感器在横向力的方向上不处于同一平面,每个传感器的受力是完全不同的,正交与斜交两种分布方式将会对传感器的受力产生影响。本文第3节中将分析两种分布的刚度以及对于横向受力的影响,选出较为合理的一种。
3 计算与分析
3.1 频率计算
频率计算采用cosmos软件进行有限元模态分析,由于下夹具与振动台连接,故约束下夹具每个安装孔的3个平动自由度,传感器分别通过4个螺钉与上下夹具相连,因此将传感器的上下表面设置为刚性连接。传感器建模外形按照实际尺寸,并修正其密度和弹性模量,使之质量和各向一阶频率与实际指标一致。经修正密度为7540kg/m3,弹性模量为4.5GPa,计算质量为10.5Kg,计算一阶横向频率为1927Hz,一阶垂直向频率为2030Hz。可见在这组参数的修正下,横向刚度基本与指标一致,由于内部结构未知,只能将其模拟为刚体,因此在弹性模量一致的情况下出现了垂直向刚度和横向刚度相差不大的情况,修正后的传感器模型满足了横向刚度,虽然垂直向刚度远小于指标值,但可以说此模型是保守的,如果将其代入整体结构进行计算,其频率也将是保守的。经计算正交分布和斜交分布的一阶频率见表2,振型见图6、7、8、9。
表2:正交与斜交分布一阶频率
图6:正交分布横向一阶振型
图7:斜交分布横向一阶振型
图8:正交分布垂直向一阶振型
图9:斜交分布垂直向一阶振型
从表2可知无论是正交还是斜交分布,其横向一阶频率都几乎达到了试验最高频率的3倍,而垂直向频率由于使用了传感器的保守刚度,其实际频率应比表格中的数值更高,因此从频率角度来说正交和斜交都可满足试验的要求。
3.2 水平向试验传感器受力情况分析
在传感器的指标中,倾覆力矩量程(Mx,My)为2600Nm,扭转力矩量程(Mz)为1550Nm。如果试验中卫星造成的倾覆力矩由8个传感器平均承担,则仅能测量2600×8=20.8KNm的倾覆力矩,这对于一般卫星试验来说显然是不够的。此外根据传感器的指标计算水平向测力可达8×60=480KN,水平向量程是否真有如此大?根据2.3节末尾的推论,FMD夹具的水平向受力情况远较垂直向来得复杂,以上两个结论到底是否正确还有待进一步验证,因此很有必要针对水平向试验的传感器受力情况进行详细分析。
由上文可知卫星质量2.7吨,质心高度1.65m,原夹具质量378Kg,试验水平向最大推力10吨,FMD夹具质量598.54Kg,试验最大量级1g。振动台推力公式如下:
F=kMA (1)
式中F为推力,k为有效质量系数,M为运动部件总质量,A为加速度。在纯加速度控制中,水平向卫星与振动台总的运动质量M=动圈(116Kg)+驱动块(50Kg)+滑板(347Kg)+附加铝板(500Kg)+夹具(378Kg)+卫星(2700Kg)=4091Kg,A=1×10=10m/s2,F=100KN,将M、A、F代入式(1),可得此卫星有效质量系数k=2.44。
在力限控制中,水平向卫星与振动台总的运动质量M=动圈(116Kg)+驱动块(50Kg)+滑板(347Kg)+附加铝板(500Kg)+夹具(598.54Kg)+卫星(2700Kg)=4312Kg,A=10m/s2,k=2.44,同样将M、A、k代入式(1),可得此卫星在力限试验中的预测最大推力为10.5吨。考虑到安全余量,将此推力放大20%,即12.6吨(126KN)作为静力分析的载荷,运用cosmos软件对FMD夹具进行静力计算。
在静力计算中约束下夹具各安装孔的3个平动自由度,载荷施加在上夹具顶部平面中心上方1.65m处,采用远程载荷多点刚性约束将载荷传递给上夹具与卫星连接的各个安装孔,传感器与上下夹具的8个螺钉连接采用刚性接头单元进行连接,以便传递力。约束状态见图10。
图10:静力计算约束状态
在分析中,分别计算各传感器与上夹具4个连接孔的三个方向的力以及其相对传感器顶面中心的力矩,然后再算出各传感器的三向合力及合力矩,经计算正交和斜交各传感器受力情况见表3,传感器序号见图4,5。
表3:传感器受力情况
由表3可知,正交分布最大X向合力为24.75KN,最大Y向合力为12.2KN,最大Z向合力为74.4KN,斜交分布最大X向合力为24.34KN,最大Y向合力为8.27KN,最大Z向合力为74.1KN,由此可见无论正交还是斜交其三个方向的合力都没有超过传感器的量程,而力矩方面都处在1KNm以下,完全不存在上述无法承担倾覆力矩的问题,能够满足试验测量的要求。此外从X向受力情况来看8个传感器的受力都不相同,当其中X向受力最大的传感器达到指标中的60KN时,其他的传感器还远没有达到60KN,因此其量程要远低于上述的480KN。
表3中的Z向合力可用于倾覆力矩的测算,其中两种分布情况受拉向的力都远大于受压向的力,这种现象根据材料力学弯矩原理说明在水平向试验中倾覆力矩中心并不处于夹具的中心,而是靠近受压端,且在真实试验中该中心呈正弦方式相对夹具中心来回摆动,并随着推力的变化其摆动幅度也将随之改变。
3.3 螺钉校核
根据以往试验的经验,水平向由于倾覆力矩的参与,螺钉在垂直向无论最大轴向应力还是最大横向应力都小于水平向,且传感器与夹具连接的方式为一端通孔、一端螺纹孔,通孔直径略大于螺钉外径,形成间隙配合,这种连接方式仅能看作普通螺栓连接而不能看作绞制孔连接。因此根据机械设计手册关于普通螺栓连接的应力校核方法,本节将着重针对传感器与上夹具连接螺钉进行轴向应力和横向应力两个方面的校核,并通过预紧力计算出螺钉的最小扭矩,最后根据扭矩校核其剪切应力。
从表3可以看出最大横向力为25.38KN,最大轴向力为74.4KN,由于两种分布方式横向和轴向最大合力区别不大,因此仅以这两个最大的数据作为校核的载荷条件。
3.3.1 轴向应力
传感器与上夹具连接螺钉为4个碳钢8.8级M16 2.0螺钉,传感器顶部平面相对于整个FMD夹具来说可简化为一点,4个螺钉的受力误差忽略不计,因此认为传感器的最大轴向力由4个螺钉均分承担,每个螺钉承受的最大轴向力F=74.4/4=18.6KN。校核螺钉轴向应力公式如下:
(2)
式中 为螺钉轴向应力;S为最大应力安全系数,在控制预紧力的情况下,S应取1.2~1.5,在此为了安全取1.5;d1为螺钉小径,查表得M16 2.0螺钉小径为13.835mm; 为螺钉的屈服极限,查表得8.8级碳钢螺钉屈服极限为640MPa;F0为螺钉总拉力,它是螺钉所受轴向载荷与剩余预紧力之和见下式:
(3)
式中F"为剩余预紧力,查表得在承受动载荷的情况下其值应取(0.6~1.0)F,为了安全取1.0F,由此可得F0=2F=2 18.6=37.2KN。将S、F0、d1代入式(2)得 =321.7MPa<640/1.5=426.7MPa,轴向应力符合安全要求。
3.3.2 横向应力
普通螺栓横向应力校核的原则为在预紧力的作用下,横向力不能使被连接工件之间发生错动,根据机械设计手册传感器每个螺钉最大预紧力公式如下:
(4)
式中F"为每个螺钉受最大横向力;k为摩擦连接可靠性因子,取值范围为1.1~1.3,为了安全取1.3;m为结合面数,由于传感器与上夹具及螺钉垫片有2面结合,因此m=2;Fw为最大横向总受力25.38KN; 为结合面间摩擦因数,对于干燥的钢铁零件取值范围为0.1~0.16,为了安全取0.1;z为螺钉个数4。将k、Fw、m、 、z代入式(4)得F"=41.243KN。
仍然运用式(2),此处F0=F",将其余数值代入得 =356.7MPa<640/1.5=426.7MPa,横向应力符合安全要求。
3.3.3 螺钉扭矩计算及校核
螺钉扭矩与预紧力简化关系式如下:
(5)
其中T为扭矩;F"为螺钉最大预紧力41.243KN;d为螺钉公称直径16mm,将F"、d代入式(5)得扭矩T=132Nm。因此在装配时只要每个M16螺钉安装扭矩不小于132Nm,就可以保证安全的预紧力。
对螺钉施加扭矩会使其产生剪切应力,因此必须对其进行校核,螺钉抗扭截面模量及校核扭转剪切应力计算式见式(6)、(7):
(6)
(7)
式中Wp为抗扭截面模量;d1为螺钉小径13.835mm; 为扭转剪切应力;T为扭矩132Nm; 为许用剪切应力,查表得在变载情况下, = /2.5=256MPa。将上述参数代入式(6)、(7)得 =254MPa< =256MPa,扭转剪切应力符合安全要求。
3.4 结论
从上述分析中我们可以看出,正交分布和斜交分布无论在频率上还是受力情况上都能满足试验的要求及传感器的指标,虽然两种分布的受力情况完全不同,但两者之间没有明显的优劣,因此对于力限FMD振动夹具的设计可任选一种分布方式,本次设计最后选择了正交分布。而传感器的连接螺钉在轴向力、横向力以及扭矩的校核中都能满足安全要求,但扭转剪切应力略显余量不足,这可以通过选择更高级别的螺钉(如10.9级)来解决。综上所述,此FMD夹具的设计及传感器选型符合力限试验的要求。
4 问题讨论
从设计到分析,可以看出大型FMD夹具设计的要点为选材、传感器数量、传感器选型、结构、螺钉配置以及加工。其中选材、传感器数量以及结构决定了整个夹具的刚度,前两者文献[4]进行了详尽的分析,并给出了重要结论,结构方面应尽量考虑安装方便,在保证必要刚度的同时尽量减轻重量、降低高度。关于传感器选型和螺钉配置决不能想当然粗略计算了事,其实际的受力情况远比想象中的复杂,必须进行详细计算后再作出选择,这样才可保证万无一失。在夹具的加工上,为了保证测量精度,各个力传感器在安装后对于上下平面的平面度要求极高,而大型FMD的上下夹具与传感器安装面的面积较大,在加工时很难做到极高的平面度,这可以通过在上下夹具安装面上设计凸台来减小其面积降低加工难度。总之大型FMD夹具在设计中必须考虑周全,计算充分才能保证性能,确保加工后一次成功。
5 总结
本文通过对某大型卫星三向力限FMD振动夹具的设计和分析,揭示了其频率特征和详细的水平向受力情况。目前国内已有多个科研院所开展了力限振动试验的研究,但大多都停留在垂直向做单向试验,传感器也仅用到单向力传感器,随着理论水平及传感器技术的不断进步,自"十一五"规划开始出现了三项力限振动试验的研究课题。本文的论述仅为一种设计计算方法,力图消除认识误区,为将来越来越多的三向FMD夹具设计打下基础。本次的设计计算还存在如摆动的倾覆力矩中心如何准确测量,从而得到真实倾覆力矩;传感器受力如超过指标应如何配置传感器;传感器模型应如何模拟才能精确的反应其各向刚度等问题,这些问题都有待进一步研究解决。