在制造企业中,有效的软件不但能缩短产品的设计周期同时还能提高设计质量。本文作者根据企业本身主导产品的技术特点,利用SolidWorks软件探索了从零件设计、部件设计到最终产品装配设计的实现方法及设计技巧,以供读者参考。
一、SolidWorks功能综述
SolidWorks软件功能强大并且易学易用,因而近年来在机械设计行业得到了广泛的应用。其功能特点主要包括如下几点:
(1) 参数化设计、特征建模技术及设计过程的全相关性使其具有很好的设计柔性,即设计过程灵活,修改方便;
(2) 全Windows特性的特征管理器使设计过程的操作及管理条理清晰,操作简单,完整的动态界面和鼠标动态控制对设计复杂零件是非常实用而且特别重要的技术手段;
(3) 功能强大的CAD模块包括了草图设计、曲面建模、实体建模和钣金零件设计等,可以完成基于特征的CAD模型建立,满足机械设计要求;
(4) 面向装配的零件设计为大型装配体的建模提供了重要的技术方法,其IPA动画制作可以实现动态模拟装配,同时可以进行运动分析,从而在计算机里完成零件设计正确与否的校验;
(5) SolidWorks是包含了CAD/CAM/CAE功能的集成化软件,全面满足设计、分析、制造、产品数据管理的一体化要求。
综上所述,SolidWorks软件的基本设计思路为“实体造型→虚拟装配→二维图纸”,三维实体建模使设计过程形象而且直观,虚拟装配可以实现设计过程的随时校验,从而避免可能造成的直接经济损失。二维图纸的自动绘制也满足了实际生产的需求,从而完全满足机械设计企业的设计生产要求,因而得到广泛的应用。
二、相关技术基础
1.参数化造型
参数化造型(Parametric Modeling,又称尺寸驱动几何造型技术)中,物体的几何外形是由受约束的数学关系式来定义的,而不仅仅取决于简单的、孤立的尺寸参数。其主要技术特点在于:基于特征,全尺寸约束,尺寸驱动设计修改以及全数据相关。
(1)基于特征 将某些具有代表性的几何形状定义为特征,并将其所有尺寸定义为可变参数,进而形成实体,以此为基础进行更为复杂的几何形体的构造;
(2)全尺寸约束 将形状和尺寸联合起来考虑,通过尺寸约束来实现对几何形状的控制。造型必须以完整的尺寸参数为出发点(全约束),不能漏注尺寸(欠约束),也不能多注尺寸(过约束);
(3)尺寸驱动设计修改 通过修改尺寸数值来驱动几何形状的改变;
(4)全数据相关 尺寸参数的修改带动其他相关模型中的相关尺寸的更新,从而驱动模型更新。
采用参数化造型进行设计,最大的优点是CAD系统会自动记录几何建模的整个过程。换句话说,系统不仅记录几何模型,同时还记录设计意图即实体间的关系。修改零件形状时,只需编辑尺寸的数值即可实现形状上的改变。
2.关联设计
在传统的CAD系统中,装配体(部件)设计大都采用自底向上的方法,即首先设计出各部分组成零件,然后再把设计好的零件拼装在一起,各零件间不存在任何关联关系。当部件功能或结构需做出调整时,相关零件的结构形式、尺寸不会自动做出相应的改变;反之,当某零件发生改变时,部件功能或结构也不会做出自动调整。零件之间的装配关系和尺寸协调完全依靠设计人员手工完成。这种CAD系统实际上仅起到了辅助制图的作用。要使CAD系统真正有效地工作,必须采用基于关联的设计方法,即以零件所包含的各种几何信息为数据源头,通过几何继承、数学推导等方式获取其他所需信息,选用适当的约束传播和求解模型,来构筑一个具有实时响应变更能力的信息资源高度共享的体系。
SolidWorks软件能很好地实现设计过程的关联性。对于存在装配关系的零件,可以建立其配合部分的尺寸关联,尺寸值可以相互驱动与影响。例如, A零件的a尺寸与B零件的b尺寸存在尺寸关系b=a+0.1,那么如果改变A零件模型中的尺寸值a,可以驱动B零件模型的同步协调改变。这样在设计过程中一方面可以提高设计效率,同时也可以避免错误。从而实现了零件之间的关联设计,对于大型装配体的三维设计具有重大的实际意义。
三、实现方法
我厂的主要产品是铁路罐车成品及相关配套部件,因此设计部门的主要工作包括零部件设计及最终的产品装配设计。由于市场竞争的日趋激烈,因此产品的种类越来越多,更新换代也越来越快,这就对设计、生产及管理提出了更高的要求。对于设计部门来说,设计效率和设计过程的准确性对于缩短产品研发周期和降低生产成本都意义重大。因此我厂对设计部门的软硬件投入力度很大,并采用了功能强大且易于掌握的SolidWorks作为产品设计的软件平台。针对工厂产品的特点,我们的设计思路如图1所示。
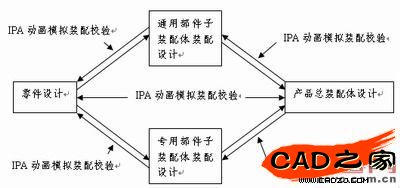
图1 产品的设计思路
具体说明如下:
(1) 零件可分为3类,一是用于通用部件的常用标准件(例如螺钉、弹簧等),二是用于某一大类产品的子零件(可视为半标准件),三是某类产品的特有零件。在分析产品的设计要求后,可以对其中的子零件进行分类管理,便于合理分工并协调设计人员甚至不同部门之间的设计进程,同时可以避免重复劳动(因为标准件和半标准件的设计可能已经完成),抓住设计任务的重点和难点,从而有效提高工作效率;
(2) 部件设计也可分为两类,一类是通用的标准结构体,这部分设计可以在平时完成并且可以适用于绝大多数总装配体。第二类是专用部件的子装配体,这部分设计是对产品设计中包含创新性的部分,因而应该特别注意其设计进度与质量,进而保证总体设计质量与效率;
(3) IPA动画装配设计校验是保证设计质量的重要技术手段,用SolidWorks的虚拟动画装配并辅助以机构运动分析,既可以对零件设计进行参数上的检查(排除人为因素的影响),又可以对整个产品的结构及功能进行合理性分析,从而有效避免方案设计和人工设计中可能存在的错误,避免更大的直接经济损失;
(4) 设计技巧。由于大型罐车产品的装配体包含几百甚至上千的零件,因此在设计过程中必须对零件进行适度的“简化”处理,否则产品的总装配体的动画仿真甚至只是简单的旋转都非常缓慢。因此在不影响整体效果的前提下,采用了如下两种方法进行处理以提高设计效率:
1)装配体中的零件显示方式有实体、线框等方式(甚至可以用参数控制零件在装配体中是否显示),对于有些非关键零件可以忽略其内部形状及细节描述,这样可以有效地降低对于计算机硬件的要求,从而使大型装配体的显示操作变得快捷而且逼真;
2)用图层设置对大装配体中的零、部件进行分类管理(单个零件的设计也应对实体、基准面及草图等相应地进行分层管理),这样对于图形显示、编辑及动画模拟等都重要的意义。零件、部件间的装配信息可以利用SolidWorks软件的Property Manager来获取,从而检查是否按照其应有的装配约束(如贴合、对齐、同轴等)进行了正确的装配操作。
四、应用实例
基于以上的设计思路及技术手段,我们在产品设计过程中采用了三维的全参数化设计方法,相对于传统的手工绘图设计及二维软件设计,不但提高了设计效率,而且提高了设计的准确性,从而实实在在地提高了产品的市场竞争力,为企业的发展注入了新的活力。
下面以我厂主导设计的铁路卧式粉状货物罐车为例,来说明其零件的参数化设计及产品的装配设计方法。
图2为罐体的参数化3D模型。罐体的主要功能是运输及装卸货物,需根据自重、载重、工作压力等来设计罐体的长度L、半径r及壁厚δ,同时设计时要考虑到它与几个盖板间的装配关系,将其作为其他零件的父零件来处理。在模型中同时建立用于装配的基准轴和基准面,而且这些特征也都是参数驱动的,并放在专用图层中。
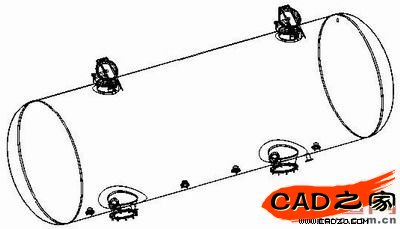
图2 罐体的参数化3D模型
图3为罐体与枕梁上盖板、牵引梁上盖板的装配图。两个盖板零件在装配树中都以罐体为其父节点,在进行参数化建模时,除了模型本身的参数驱动外,还应建立其与父零件(罐体)之间的参数关联:枕梁上盖板及牵引梁上盖板的半径等于罐体半径加上罐体壁厚。同时建立用于装配的基准轴及基准面,在进行装配建模时,通过与罐体的轴向同轴约束及基准面的贴合约束,就可以建立参数化的装配模型,同时罐体半径的改变可以传递并且驱动两个盖板模型的更新。
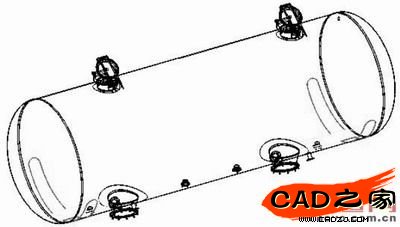
图3 罐体与枕梁上盖板、牵引梁上盖板的装配图
图4为罐体装配与车体其他部分的最终装配效果。由于在零件建模时采用了图层管理及良好的参数控制,因此装配校验变得非常简单而且明晰,通过图层的关闭、装配树中对零件的抑制与反抑制等方法来控制零件及部件(专用和通用)的显示,通过参数的关联、传递、模型驱动及IPA方法来检验设计结果,从而保证零件设计与装配设计之间的协调一致,并且通过IPA动画模拟还避免了部件之间可能发生的干涉。
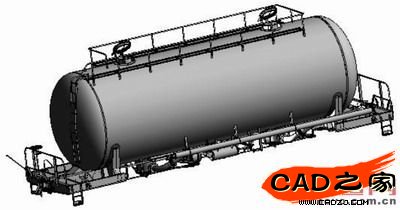
图4 罐体装配与车体其他部分最终装配效果
五、结论
通过CAD软件及相关设计技术的应用,我厂的产品设计周期大大缩短,设计质量也得到了显著提高,从而提高了本企业产品的市场竞争力,取得了显著的社会效益和经济效益。