汽车车灯侧灯纹的数控加工
时间:2011-05-22 16:27:25 来源:未知
<%end if%>
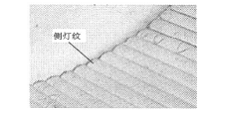
图1 侧灯纹
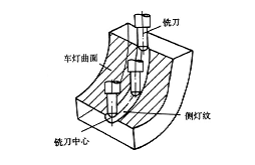
图2 侧灯纹切削示意图
1 引言
在对汽车车灯进行实体造型的过程中, 灯罩以及车灯的侧面经常遇到如图1所示的侧灯纹。对于这种侧灯纹的加工, 目前采用的方法是每一条侧灯纹利用数控铣刀一次加工成型, 如图2所示。由此可见, 侧灯纹造型并不需要建立完整的3D 模型, 只需生成加工侧灯纹过程中代表铣刀中心运动轨迹的空间曲线, 然后根据生成的空间曲线进行数控编程。
因此侧灯纹的加工分为2个步骤: 轨迹曲线的建模(即造型)和数控加工程序的生成。由于每一条侧灯纹的铣刀中心运动轨迹都单独位于一个平面之内, 目前的造型方法其实就是平面与曲面求相交曲线。轨迹曲线生成之后, 设计合理的进刀和退刀路线,将曲线按一定要求离散成点集,选择数控加工工艺参数,利用手工编程生成数控加工程序。
由此可见,侧灯纹的加工完全是重复性的工作,加工效率比较低下,尤其是生成数控加工程序阶段,若侧灯纹数量和每条轨迹曲线的离散点都较多, 则手工编程的工作量将十分惊人。
下面介绍基于UG二次开发环境, 利用二次开发语言opengrip ,实现侧灯纹的轨迹曲线建模和数控加工程序的自动生成。
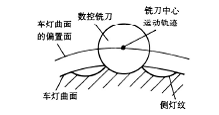
图3 侧灯纹加工原理示意图
2 侧灯纹生成的基本原理
图3 为侧灯纹加工原理示意图, 图中的圆代表数控铣刀, 圆心代表铣刀中心的运动轨迹。由图3可见, 一般情况下, 侧灯纹剖面的形状是个角度小于180°的圆弧, 因此加工侧灯纹的铣刀中心运动轨迹并不位于车灯曲面, 而是位于车灯曲面的偏置面。每一条侧灯纹的铣刀中心运动轨迹都单独位于一个平面之内, 因此侧灯纹轨迹曲线的建模归根到底就是一连串平面与车灯曲面的偏置面求相交曲线。
侧灯纹的分布一般符合一定的规律, 因此铣刀中心运动轨迹所在的平面也按照某个准则。绝大多数情况下, 铣刀中心运动轨迹所在的所有平面都平行于脱模线,从而确保侧灯纹不产生倒脱模现象。
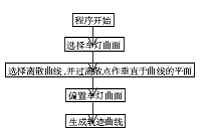
图4 轨迹曲线建模流程图
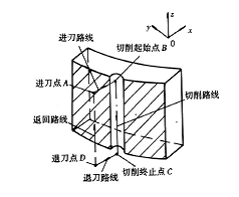
图5 侧灯纹切削循环示意图
3 侧灯纹自动生成程序的开发过程
UG提供多种二次开发语言,open grip 就是其中之一。与其他的二次开发语言相比,open grip 具备简单、方便、交互性能强等优点。
由于侧灯纹的制造分为2 个阶段, 因此本程序也分为两大部分: 轨迹曲线的建模和数控加工程序的生成。在轨迹曲线建模完毕之后将产生一个对话框,供用户选择是否生成数控加工程序,若选择生成数控加工程序则继续,否则结束程序。
- 轨迹曲线的建模
- 一般情况下, 单个曲面与平面交线只产生1 条空间曲线,但有时产生曲线的数量不止1 条,例如环形曲线与平面相交,很有可能产生2 条曲线。
- 绝大多数情况下, 车灯曲面的偏置面不是单个面,可能有几个甚至几十个曲面组合而成,因此平面与这些曲面相交的情况可能非常复杂。这些曲面中, 有些曲面和平面没有交线, 有些和平面有交线,但交线的数量不能确定。因此, 这一步骤的难点在于在所有相交曲线中寻找真正代表铣刀中心运动轨迹的交线。图4 为轨迹曲线建模阶段的程序流程图。
#p#分页标题#e#- 数控加工程序的生成
- 图5 为侧灯纹切削循环示意图。侧灯纹的加工过程不只包括数控铣刀在曲面的切削过程, 它还包括切削之前的进刀过程, 切削之后的退刀过程和返回过程。全部4 个过程位于同一个平面之内。
- 因此,加工每条侧灯纹,数控铣刀的走刀路线应该是A →B →C →D →A。A 点代表每一循环的进刀点即铣刀的出发点, B 点代表开始切削曲面的起始点, C 点代表结束切削曲面的终止点, D点代表每一循环的退刀点。执行完1个循环,结束1条侧灯纹的加工, 数控铣刀从这个循环的进刀点A 转移到另1个循环的进刀点,开始另1 条侧灯纹的加工。
- 切削循环的切削路线实际上就是轨迹曲线建模选择车灯曲面偏置车灯曲面生成轨迹曲线程序开始选择离散曲线,并过离散点作垂直于曲线的平面阶段生成的相交曲线, 切削起始点B 和切削终止点D 在轨迹曲线建模之后就确定下来。而进刀过程、退刀过程和返回过程由于数控铣刀处于空运行阶段, 所以这3个过程铣刀的走刀路线都为直线, 因此确定进刀点A和退刀点D成为每个加工循环的关键,得到A点和D点之后,进刀路线、退刀路线和返回路线就能确定。此外, 加工过程中铣刀不能与车灯模具发生干涉, 因此所有加工循环的进刀点和退刀点都必须位于车灯曲面的同一侧。
- 解决的方法是在每一个循环过程中设立1 个临时坐标系, 所有临时坐标系的某个坐标轴(如图5所示的x 轴) 的正方向都位于曲面的一侧。在每个临时坐标系下读取B 点的坐标值, 然后对坐标轴正方向一致的坐标值加上或减去进刀距离(图5中应该选择x 坐标值减去进刀距离) , 其他2 个坐标值不变,通过此3 个坐标值就能确定进刀点A。同理,由C 点得到D 点。最后取消临时坐标系,返回工作坐标系, 由工作坐标系确定生成数控加工程序时的A、B 、C、D 4 点以及相交曲线离散的点集的坐标值,最后由这些坐标值生成数控加工程序。生成的数控加工程序只需按加工工艺修改某些参数, 如刀具转速、进刀速度、冷却液开关的控制等就能送入数控机床进行加工。图6 为数控加工程序生成阶段的程序流程图。
- 程序自动运行生成数控代码之后, 将在屏幕上显示代表每个加工循环数控铣刀走刀路线的曲线和直线, 用户可通过这些曲线和直线来检验生成的数控代码是否正确, 数控铣刀与车灯模具是否会发生干涉。
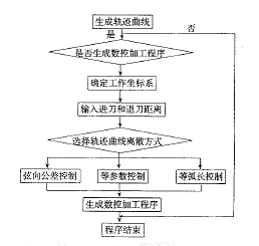
图6 数控加工程序生成流程图
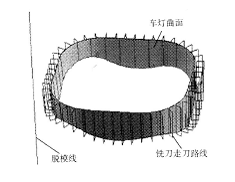
图7 侧灯纹数控加工刀路示意图
4 应用实例
以下是一个汽车车灯侧灯纹的轨迹曲线建模的应用实例。车灯曲面共有32 个,曲面的偏置距离为1mm,侧灯纹数量50 条。
由试验可得, 手工对平面与车灯曲面的偏置面求轨迹曲线,则每生成一条轨迹曲线大约需30 s ,因此生成50 条轨迹曲线大约需要25 min ; 若采用此程序实现所有轨迹曲线的建模则大约只需要30 s。图7为此侧灯纹数控加工刀路示意图。图7中不仅显示每条侧灯纹加工时数控铣刀切削时的轨迹曲线, 还包括每个加工循环过程中铣刀的进刀、退刀和返回路线。
在数控加工程序生成阶段, 若每条轨迹曲线离散成10点, 再加上每个加工循环的进刀点和退刀点,因此每个切削循环共有12个点,加工50条侧灯纹共需生成600个点。采用手工进行逐点编程,则需要1h 左右, 且容易出错, 若采用此程序自动生成,大概只需要5s。
由此可见, 该程序对于侧灯纹加工效率的提高非常显著。
5 结束语
基于汽车车灯侧灯纹加工的基本思路, 利用UG/ opengrip 二次开发语言,实现了侧灯纹的轨迹曲线建模和数控加工程序生成的自动化。实验证明,该程序能极大地提高侧灯纹的加工效率。
但该程序在多个方面还存在一定的局限性, 主要有以下2 点:
#p#分页标题#e#- 对汽车车灯曲面造型技术的要求相对较高,曲面之间不允许出现较大的空隙。
- 在某些特殊情况下,有些加工循环临时坐标系的控制容易出错, 导致铣刀进刀和退刀路线与车灯曲面的相对位置不一致, 从而影响数控加工程序的生成。