数控加工技术已广泛应用于模具制造业,如数控铣削、镗削、车削、线切割、电火花加工等,其中数控铣削是复杂模具零件的主要加工方法。数控设备为精密复杂零件的加工提供了基本条件,但要达到预期的加工效果,编制高质量的数控程序是必不可少的,这是因为数控加工程序不仅包括零件的工艺过程,而且还包括刀具的形状和尺寸、切削用量、走刀路径等工艺信息。对于简单的模具零件,通常采用手工编程的方法,但大多数模具的型芯和型腔,往往都具有比较复杂的曲面,要加工这样的曲面,手工编程是难以完成的,往往需要借助于CAM软件编制加工程序,如Pro/Engineer、UG、Cim atron、M asterCAM等。M asterCAM软件是美国CNC Software公司开发的基于PC平台的CAD/CAM系统,由于它对硬件要求不高,并且操作简单方便、易学易用并具有良好的性能价格比,因而深受广大企业用户和工程技术人员的欢迎,广泛应用于机械加工、模具制造等领域,它具有二维几何图形设计、三维曲面设计、刀具路径模拟、加工实体模拟等功能。从而实现了从产品的几何设计到加工制造的CAD/CAM一体化,是目前世界上应用最广泛的CAD/CAM软件之一。下面结合一个典型的冲模零件介绍利用CAM软件进行数控编程过程与应用的特点。
1 零件加工工艺分析
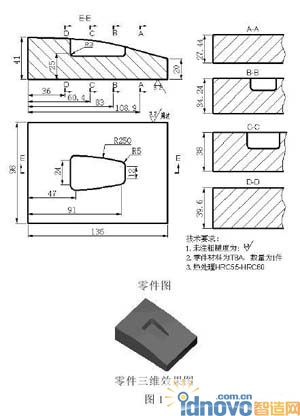
图1为所要加工的凹模零件图和三维图形。在运用M as-terCAM软件对零件进行数控加工自动编程前,首先要对零件进行加工工艺分析,确定合理的加工顺序,在保证零件的表面粗糙度和加工精度的同时,要尽量减少换刀次数,提高加工效率,并充分考虑零件的形状、尺寸和加工精度,以及零件刚度和变形等因素,做到先粗加工后精加工;先加工主要表面后加工次要表面,先加工基准面后加工其他表面。
为了减少零件在数控铣床上的加工时间,提高数控铣床的利用率,首先安排零件的六个表面在普通机床上加工,周边四个平面加工到尺寸,上平面留0.5m m的加工余量,底面加工平整光滑。由于零件的六个表面在普通机床上加工比较简单,在此不再说明。
下面重点说明零件在数控机床上加工型腔和曲面部分加工路径的编辑。
2 凹模型腔和曲面加工路径的编辑
2.1粗加工内槽
在不影响零件后续加工的情况下,为了减少换刀次数,安排内槽粗加工工序在曲面粗加工之前。
加工对象的形状特征:零件内槽从俯视角度看是一个近似梯形的形状,内槽底面是平面,底面与侧壁有R3的圆角过度,侧壁的四个面有R5的圆角过度。
选用刀具:刀具大小的选用原则为刀具半径ρ≤(0.8~0.9)×曲线的最小曲率半径r,故选用的刀具直径为!8m m;由于是粗加工,需要去除大量的余料,如果选用球头铣刀,因其刀头处刃口单薄,容易磨损,且加工效率低,故不适合用于粗加工。经综合考虑,选用直径!8m m的平头铣刀比较合适。下刀方式有两种:第一,加工时不能将平头铣刀当作钻头用(直接去除材料垂直下刀),故在进行这一工序前,先安排在下刀点处钻孔,孔的直径大于或等于本工序用的刀具直径,然后在孔位处直接垂直下刀进行粗加工内槽,但由于是内槽加工,所以要选用键槽铣刀;第二,该零件内槽是封闭的,如果在粗加工内槽前不预先钻孔,则必须选用键槽铣刀并采用螺旋方式下刀。
加工方式:根据下刀方式不同可选用两种———曲面挖槽粗加工(直接垂直下刀,配合第一种下刀方式进行)、曲面挖槽粗加工(螺旋式下刀,配合第二种下刀方式进行),图2是两种加工方式的刀具路径。经对比分析,不难发现前一种方式相对后一种来说,具有路径清晰、走刀路程短、下刀切入点容易控制等优点,下刀方式选用第一种,加工时选用直接垂直下刀的曲面挖槽粗加工的加工方式更合理。
2.2粗加工曲面
加工对象的形状特征:该曲面只在X方向弯曲,在Y方向是直线的,且沿着X的负方向曲面的Z坐标是单调递增的。选用刀具:根据这样的形状特征,选用平头铣刀,为了提高加工效率,可定为直径"20m m的平头铣刀。
下刀方式:由于该曲面加工可从切削范围外切入,故下刀方式是在切削范围外直接垂直下刀。
加工方式:有两种加工方式———曲面挖槽粗加工、平行式粗加工,图3分别是这两种加工方式的刀具路径,经对比分析曲面挖槽粗加工路径简洁、减少许多不必要的退刀和抬刀、走刀路程短,故选用曲面挖槽粗加工方式比较合理。
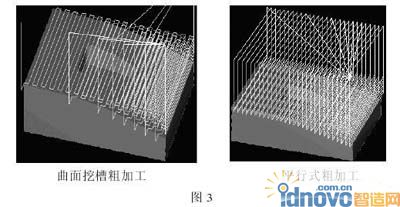
2.3精加工曲面
下刀方式:与粗加工该曲面一样,可在切削范围外直接垂直下刀。
加工方式:有两种加工方式———等高外形精加工、平行式精加工。图4是两种加工方式的刀具路径,从图上分析可知:要将曲面精加工光滑,等高外形精加工必须选用球头铣刀,并且,由于曲面的曲率不同,造成走刀行距不均匀,加工出的曲面粗糙度不同;平行式精加工可选用圆角刀或平头铣刀,从加工效率角度考虑,平行式精加工刀路简洁,且走刀行距均匀,选用此方式比较符合曲面形状特征。
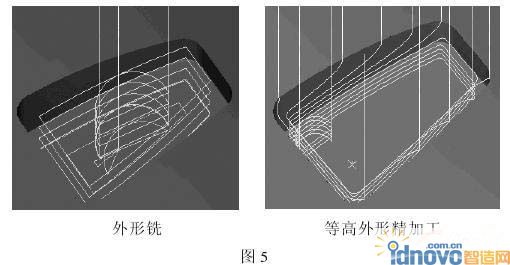
选用刀具:根据该曲面的形状特征,如果刀具只沿X方向走刀,那么要精加工该曲面就可以选用平头铣刀,不必选用球头铣刀,就可以把该曲面加工光滑;如果刀具是矩形回转式走刀或是只沿着曲面的直线方向走刀(图1的Y方向),那么要精加工该曲面,必须选用球头铣刀,球头铣刀在加工时刀尖点的切削速度为零,导致选用的走刀速度不能过快,极大地影响了加工效率。由于加工方式确定为平行式精加工,故选用刀具是平头铣刀,为了减少换刀次数,刀具规格与上一工序一样。
2.4精加工内槽侧壁及槽底圆角
选用刀具:由于内槽侧壁与槽底面有R3的圆角过度,故为了同时精加工该圆角,选用直径#6m m的球头铣刀。
下刀方式:由于大量的余料已在粗加工时去除了,在精加工时下刀方式可直接在槽的中间附近垂直下刀;为了避免在内槽侧壁留有切入点刀具痕迹,切入方式选用圆弧切线切入。
加工方式:可选用两种———外形铣、等高外形精加工,图5是两种加工方式的刀具路径,经对比分析,不难发现前一种加工方式相对后一种来说,有路径清晰、走路程短、内槽侧面切入点处可以用切线切入等优点,故选择外形铣加工方式更合理。
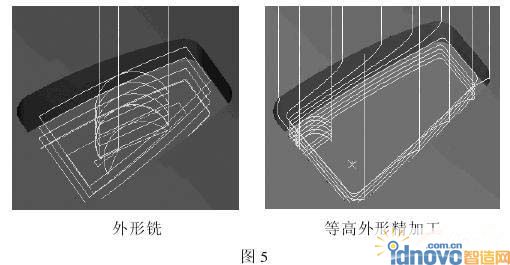
2.5精加工内槽底面
选用刀具:由于内槽底面是平面,故选用平头铣刀;内槽侧壁有R5的圆角过度,为了把底平面精加工完整,选用的刀具半径最好稍小于内槽侧壁的过度圆角半径R5,综合考虑,选用直径$8m m的平头铣刀。
下刀方式:由于大量的余料已在粗加工时去除了,在精加工时下刀方式可直接在槽的中间附近垂直下刀。
加工方式:内槽底面是平面,故精加工该平面可选用曲面加工中的浅平面精加工,加工刀具轨迹如图6所示。该加工方式对于精加工曲率半径不大的平缓曲面(包括水平面)具有特别的优点:能自动寻找出包含在设定的倾斜角度范围内的曲面,然后专门对些曲面进行加工。
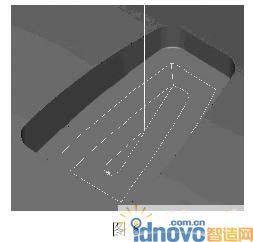
3 零件的加工仿真
设置好刀具加工路径后,利用M asterCAM系统提供的零件加工模拟功能,能够观察切削加工的过程(如图7所示),可用来检测工艺参数的设置是否合理,零件在数控实际加工中是否存在干涉,设备的运行动作是否正确,实际零件是否符合设计要求。同时在数控模拟加工中,系统会给出有关加工过程的报告。这样可以在实际生产中省去试切的过程,可降低材料消耗,提高生产效率。
4 生成数控加工指令代码及程序传输
通过计算机模拟数控加工,确认符合实际加工要求时,就可以利用M asterCAM的后置处理程序来生成NCI文件或NC数控代码,M asterCAM系统本身提供了百余种后置处理PST程序。对于不同的数控设备,其数控系统可能不尽相同,选用的后置处理程序也就有所不同。对于具体的数控设备,应选用对应的后置处理程序,后置处理生成的NC数控代码经适当修改后,如能符合所用数控设备(铣床或加工中心)的要求,就可以输出到数控设备,进行数控加工使用。
5 结束语
采用M asterCAM软件能方便地进行零件数控加工编程,并迅速自动生成数控加工程序,缩短编程时间。对于上面所述实例,该零件是模具零件中的典型形状,其典型意义表现在两方面:第一,零件曲面只有一个方向是曲线,而另一个方向是直线,对于这类具有代表性的典型曲面形状,精加工时采用的加工方法往往是平行式精加工,用这种方法来加工该类曲面,具有走刀路径简洁、走刀行距均匀的特点;第二,零件内槽的侧壁是平面,对于这类内槽的加工,粗加工往往采用二维挖槽加工,精加工采用的是外形铣,用这种方法,可以解决加工内轮廓下刀难的问题,同时具有刀路简洁,走刀路径容易控制等特点。
相关文章
- 2021-09-08BIM技术丛书Revit软件应用系列Autodesk Revit族详解 [
- 2021-09-08全国专业技术人员计算机应用能力考试用书 AutoCAD2004
- 2021-09-08EXCEL在工作中的应用 制表、数据处理及宏应用PDF下载
- 2021-08-30从零开始AutoCAD 2014中文版机械制图基础培训教程 [李
- 2021-08-30从零开始AutoCAD 2014中文版建筑制图基础培训教程 [朱
- 2021-08-30电气CAD实例教程AutoCAD 2010中文版 [左昉 等编著] 20
- 2021-08-30电影风暴2:Maya影像实拍与三维合成攻略PDF下载
- 2021-08-30高等院校艺术设计案例教程中文版AutoCAD 建筑设计案例
- 2021-08-29环境艺术制图AutoCAD [徐幼光 编著] 2013年PDF下载
- 2021-08-29机械AutoCAD 项目教程 第3版 [缪希伟 主编] 2012年PDF