1、引言
模具行业是现代制造业的重要组成部分,其面向的产品更新很快。随着我国现代汽车制造技术的发展,汽车装饰件也向塑料化方向发展,汽车注塑模具也呈现高效化、精密化、长寿命发展趋势,因此模具设计制造者为适应这一变化必须采用先进的设计制造方法,采用CAD/CAM一体化技术实现模具的设计与制造。DELCAM PLC 是全球五家最大的CAD/CAM软件供应商之一,DELCAM软件中的PowerSHAPE系统是曲面与实体相结合的复合建模系统,实现了曲面与实体间融合,特别适合于复杂形体的产品及模具的设计。基于该系统的DELCAM-Toolmaker模具设计专家系统更具有拔模面、分模面及电加工电极等模具行业专业化功能,系统的易学易用性突出,非常适合模具设计人员使用[1]。本文以汽车内衬盖(如图1)为例介绍DELCAM-Toolmaker在汽车注塑模具设计中的应用。
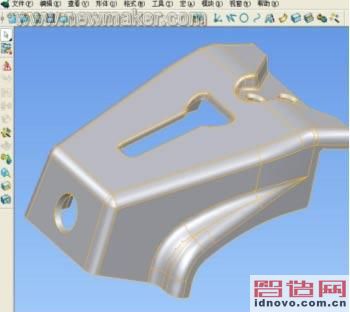
图1 塑件模型
2、利用PowerSHAPE建立塑件模型
PowerSHAPE软件能够快速、灵活地构造与编辑几何元素;独特的曲面设计、编辑工具,能完成其它CAD系统不能实现的复杂曲面设计操作,如复杂圆角、曲面调配、曲面缝补、曲面局部点位、切矢和法矢控制等;强大的复合曲面、实体设计功能,对同一组形面,既能以实体方式进行运算,又能按曲面方式进行编辑设计。通过曲线网格、分离曲线产生曲面,线框产生填充曲面及驱动曲线曲面,挤出曲面,旋转曲面,圆倒角曲面,通过实体命令中的从已选曲面产生实体,并运用实体的交、并、减、分、增厚、抽壳等操作完成塑件的造型设计,也可以利用其它软件进行塑件CAD造型,再通过DELCAM软件的DELCAM-Exchange强大的数据转换功能,将产生的CAD模型数据直接读进来,比如IGES、STL、DWG、DXF等通用数据格式及UG、Pro/E、Catia、Cimatron等高端软件的专用数据,实现数据的无品模型在导入后,可能会存在一些由于设计缺失而产生的不完整的面和间隙,要修补这些面需要花费设计者大量时间[2]。尤其是复杂的零件,DELCAM-Toolmaker能自动识别这些缺陷并进行修补,这将大大节省设计者的宝贵时间。需要注意的问题是PowerSHAPE软件是曲面与实体相结合的复合建模系统,虽然实现了曲面与实体间的融合,但所生成的实体往往需要密封处理(如图2)才能进行进行模具结构设计。有时需要进行多次密封处理才可以进行下一步,否则会产生错误的分析,这对我们不利。
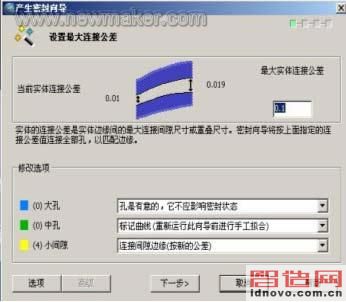
图2 实体密封
3、模具结构设计向导生成基本模架
模型完成后,生成型腔和型腔镶嵌块是进行模具设计的第一步,首先激活PowerSHAPE系统的Toolmaker模块,启动型腔/型芯向导后,点击运行自动模具镶嵌块向导(Die Wizard),框选模型,在弹出窗口中点击产品,这样向导就会自动分析运算,根据产品结构,自动找出模型的分模线,自动产生填充面填补靠破面,自动产生高质量的分模面,并自动将模型分为两部分,节省型芯和型腔的准备时间。即使是形状特别复杂的零件,也可找出大部分的分模线,提高工作效率。如图3所示向导找出的分模线,需要选择适合的分模线,我们选取第二条分模线。点击下一步可选择塑件材料,设定好收缩率,软件会对型腔和型芯进行自动缩放,并计算出模型所需的镶块尺寸。自动产生的分模面,当出现不合理时(见图4),需要进行改动,通过高级分模选项,插入相关点后,设定分离方向,使分模面更符合实际(见图5)。点击下一步设定镶嵌块的高度及圆角的处理。至此镶块设计完成,可以通过分离型芯和型腔观察结果,见图6所示。
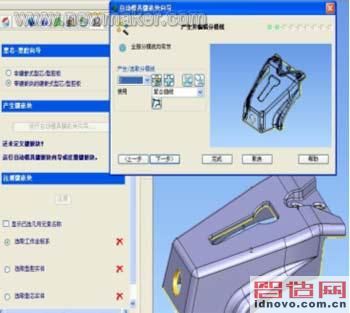
图3 分模线
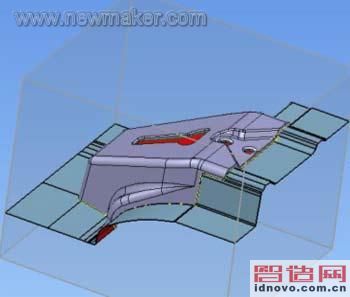
图4 向导生成的分模面
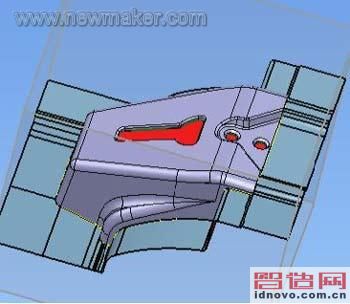
图5 修改后的分模面
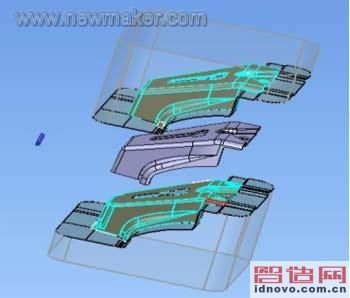
图6 型芯和型腔分离
依据向导提示,按次选择镶块的坐标系及型腔和型芯,相当于进入模架向导,在树视窗里就会自动产生一个装配文件Moldbase,内含有装配关系的子文件DW_CAVITY和DW_CORE。选取HASCO 模架,型腔板和型芯板的类型选取K20,材料选取1730。点击层会发现软件已经把将要产生的零件进行了分层,包括浇口套、定位圈、镶块、推板、支架、导柱、导套、螺钉等,见图7所示。继续向导根据塑件形状定义模架及动定模板的尺寸,我们选择模架尺寸为196×396,型腔板96mm,型芯板56mm,镶嵌块垂直位置定义方式选择D2和G,分别输入18.72和0.1,这是设置镶块在型腔和芯板中的尺寸,用来固定镶嵌。在本例中有侧向孔,故应当设置侧型芯。在当前窗口滑块标签列中,点击插入滑块机构,目的是使其在型腔处产生一个镶嵌块,启动侧型芯向导,在分模面选项选择滑块在型芯上,模具镶嵌块区域在型芯和型腔中用单个面选择好所在的区域。在倒勾型区域面(Undercut Region selection)选项中,用凸面区域(Convex Region)选取方式选择我们要做抽芯处理的凸台。点击下一步,设置好接触轮廓的各参数。依次设好侧型芯长度、调整好分模面,即完成侧抽芯向导。结果如图8所示。Tool- maker允许对已经生成的型芯(Core)和型腔(Cavity)的部件进行修改,并且这种基于装配关系下的修改不会影响模具整体布局,所有更新都将自动完成,极大地方便了设计者的修改。如果我们对已经生成的侧型芯进行修改,方法如上述步骤选取已经生成的侧型芯,选好分模面及倒勾形区域,单击完成即可。如果是一模两腔式,在设计另一个侧型芯时,需强调一点,必须事先设定好坐标系,Z应指向侧型芯运动方向。如图8所示坐标系方向。
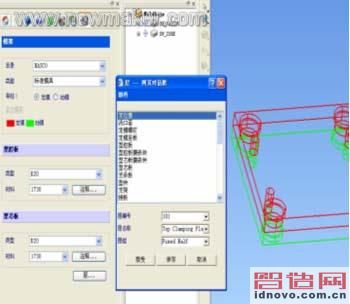
图7 分层
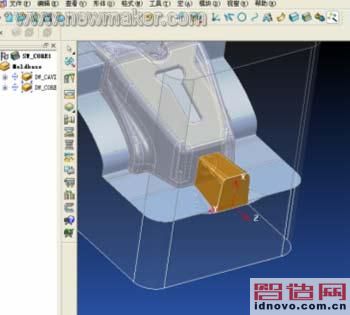
图8 侧型芯
完成型腔与型芯向导后,启动模架向导,使用此向导可指定模架类型、模板尺寸,并确定与模架相关部件的尺寸,如导柱、螺纹、浇口套等。如上一向导选HASCO的196×396标准模架等。依据本零件特点,取消支承板,选择定位圈尺寸100mm,点击下一步,进入模架向导运行成功页面,如图9所示,表格内模架基本参数全部完成,如要修改可回退进行。点击完成,系统自动进行运算,并将各模板及相关部件分置在不同的层中,每个相关部件都有装配关系,而且能将动、定模部分与镶块分成组,如图10所示。这些功能为设计者极大的减少了工作量,加快了设计速度。
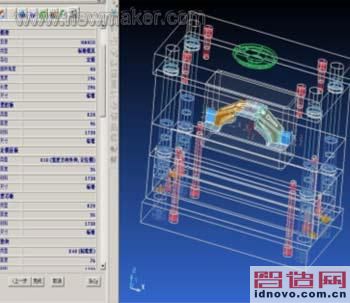
图9 模架参数
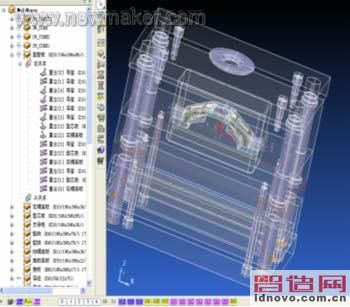
图10 模架装配树
4、注塑模的其它部件
基本模架完成后,可从软件自带的部件库里增加相应的标准部件,如浇口部件、冷却件、脱模件等。这些工作可以通过Toolmaker的部件向导来完成,通过点击下一步就可完成。对于我们所设计模具不规则的产品,通常脱模用的零件长度不一,Toolmaker提供了一个很方便的功能,利用Power Feature裁剪功能可将销、套部件裁剪到型芯或型腔,并自动完成更新。自动将几何特征增添到模具系统,它让我们再也不用手工裁剪模板上的顶针孔、沉头孔和让位结构等。比如选择顶针进行裁减系统会自动裁减出了顶针的 位置,并且自动留出配合间隙。结果见图11所示。
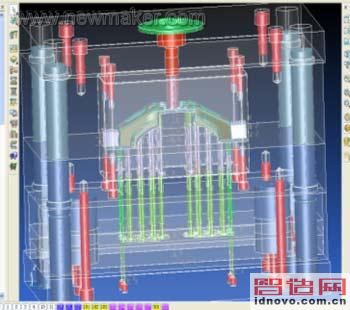
图11模具结构图
5 模具的加工
整体模型设计完毕后,可将模板提交给Delc am的加工软件进行加工孔的钻孔刀具路径及型芯、型腔和二维特征的刀具路径[3]。PowerMill的加工策略很丰富,比如我们可以将高速铣的一些加工策略、准则,合理地有选择地运用于非高速铣中,缩短加工时间,提高加工质量等,这些在此就不一一赘述了。
6、结束语
Delcam软件的ToolMaker在汽车注塑模具设计中的应用,是走向现代设计和制造的成功典范,使广大的工程设计、制造人员从繁杂的手工绘图中解脱出来,便设计和制造工作更加人性化,轻松而富有活力。
参考文献
1 韩永军.PowerMILL与模具高速加工技术[J].现代制造,2003,(12):103-105
2 杨应龙.Delcam软件在塑料注射模设计和制造中的应用[J].制造技术与机床,2003,(11): 53-55
3 罗云华,王义林.汽车模具的三维造型与数控加工[J].模具技术,2000,(4):45-47(end)
相关文章
- 2021-09-08BIM技术丛书Revit软件应用系列Autodesk Revit族详解 [
- 2021-09-08全国专业技术人员计算机应用能力考试用书 AutoCAD2004
- 2021-09-08EXCEL在工作中的应用 制表、数据处理及宏应用PDF下载
- 2021-08-30从零开始AutoCAD 2014中文版机械制图基础培训教程 [李
- 2021-08-30从零开始AutoCAD 2014中文版建筑制图基础培训教程 [朱
- 2021-08-30电气CAD实例教程AutoCAD 2010中文版 [左昉 等编著] 20
- 2021-08-30电影风暴2:Maya影像实拍与三维合成攻略PDF下载
- 2021-08-30高等院校艺术设计案例教程中文版AutoCAD 建筑设计案例
- 2021-08-29环境艺术制图AutoCAD [徐幼光 编著] 2013年PDF下载
- 2021-08-29机械AutoCAD 项目教程 第3版 [缪希伟 主编] 2012年PDF