1 概述
悬臂类实心铝型材模具,三面悬空,一面为悬臂,悬臂受力大,在挤压过程中长时间的高温高压、激热激冷、反复循环应力的作用;偏心载荷和冲击载荷作用;高温高压下的摩擦作用。及其容易引起疲劳断裂,从而使模具报废失效。利用Altair公司的挤压仿真软件HyperXtrude的强度分析功能,可以准确的计算出模具在挤压过程中的模具所受的应力场和应变场。从而可以用来分析大悬臂的平模设计的厚度和悬臂位置断裂的危险临界应力值之间的关系。并通过实际模具使用跟踪,找到其应力值与挤压制品实际通过吨数之间的相应关系,通过其相对应的关系,指导模具设计所需要取模具厚度的最佳值。在满足生产需要的强度的情况下,尽量节约模具材料,降低模具使用成本。
2 挤压模具使用的材料,工作条件及失效的主要原因
通常在挤压铝合金制品时,模具要承受长时间的高温高压、激热激冷、反复循环应力的作用;偏心载荷和冲击载荷作用;高温高压下的摩擦作用。因此,铝型材挤压模具的主要失效形式有磨损超差、铝型材与模具材料的粘着磨损、疲劳断裂、龟裂等。
H13钢是空冷硬化热作模具钢,属超高强度钢。它具有良好的淬透性、热强性、耐磨性、塑性及较高的冲击韧性、抗冷热疲劳性、热处理变形小,抗裂纹扩展性好,挤压的型材表面粗糙度好,修模省力,使用寿命长,这些特征标准是铝型材挤压模具的最好材料。
3 优化挤压模具厚度设计过程
对于悬臂类实心铝型材挤压模具的厚度直接影响模具的强度,模具的强度直接影响挤压制品的通过量和制品尺寸。模具强度确实是越厚越好,但是对于模具制造和挤压使用过程而言模具却是越薄越好,模具越薄越容易加工,模具越薄在挤压过程中所受的摩擦力也越小。同时模具减薄可以有效的节约模具材料,降低成本。
3.1设计试验方案
根据如下断面图(图1),结合挤压模具基本设计方法导流孔与断面形状相似,工作带按同心圆原则结合断面壁厚的原则。可得到如下的设计方案模具为φ227×(x+80)其中x为型模厚度(图2):
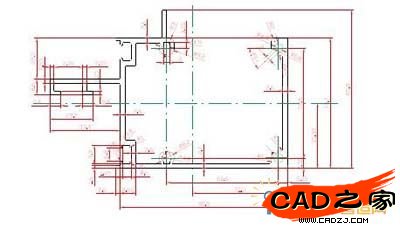
图1 试验用断面图
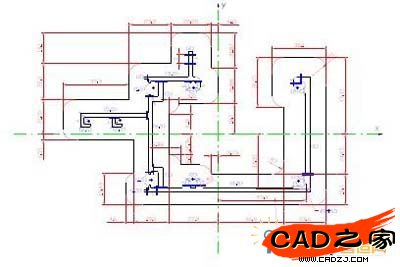
图2 挤压模具型模设计图
根据模具设计图纸,分别取型模厚度为:(1)30mm;(2)60mm;(3)80mm;(4)100mm配合80mm的专用模垫,再根据不同的厚度型模和专用模垫的组合,建立建立精确的三维模型如(图3)。
图3 挤压模具三维模型
把三维模型导入有限元分析软件HyperXtrude中,进行网格划分,得到如下图的模型(图4),并加入具体的挤压工艺参数(如表1),提交进行有限元分析计算。可得到如(表2)所示的结果。
图4 有限元分析准备模型
表1 挤压工艺参数
表2 挤压仿真分析结果
3.2 模拟结果分析
根据分析结果可以分别得到,当型模厚为30mm时:其最大应力值808Mpa,模具整体变形最大值为0.35mm;当型模厚度为60mm时:其最大应力值为654Mpa,模具整体变形最大值位0.27mm;当型模厚度为80mm时:其最大应力值为573Mpa,模具整体变形最大值位0.17mm;当型模厚度为100mm时:其最大应力值为516Mpa,模具整体变形最大值位0.16mm。这些最大应力值都出现在悬臂的根部,表明根部是最容易断裂的危险截面处。而变形最大的地方则相反在悬臂的最尾端,容易造成尺寸的偏离,顾在设计时要预偏其壁厚,以拟补变形引起的壁厚偏小。由上面得到的壁厚和最大应力值,以及壁厚和变形量之间的关系制成图标可得到如下表3的关系。
表3 型模厚度与最大变形量的关系
3.3 优化设计
由表2和表3的曲线可以很明显的看到其变化趋势,1、随着模具厚度的不断增加其模具所受最大应力值不断减小,开始是减小趋势快,到后面趋于缓慢;2、随着模具厚度的不断增加其模具的最大变形量不断减小,开始趋势比较快,后面趋于缓慢。由此可见当从模具应力和变形来看,模具厚度是越厚越好,当其材料使用也最多,费用最高。顾从成本和模具强度双重考虑选择型模厚度为80mm比较合理。
3.4 结果跟踪
按照试验方案分别制作模具型模厚度为30mm一片;型模厚度60mm两片;型模厚度80mm两片;型模厚度100mm一片;模垫厚度为80mm三片。跟踪挤压结果分别记录其上机挤压通过量。30mm的型模一上机就断裂,直接报废;60mm的型模分别通过8T和11T后模具产生裂纹报废;80mm的型模分别通过30T和32T,由于面粗划痕等表面质量原因,模具报废;100mm的型模通过34T,由于面粗等表面质量原因,模具报废。数据整理如下表。
表4 型模厚度与其通过量的关系
分析表4,取60mm的型模1和模2的平均值为9.5T;取80mm的型模的平均通过量31T。根据模具厚度与其通过量关系制成(图表5)。
由此可见模具厚度越厚其通过量越高,模具厚度不够是容易断裂失效,模具厚度到一定值时,挤压产品通过量随着厚度增加而增加缓慢,容易以表面粗、划痕或尺寸超差等形式失效使模具报废。
4 结论
a、试验结果表明模具厚度越厚其模具应力值越小,变形也越小,实际挤压通过量越大;模具厚度的不断增加到一定值后其应力和变形减小缓慢;模具厚度的增加到一定值后其挤压通过量增加缓慢甚至不增加。顾本次试验模具厚度取80mm比较合理。
b、利用Altair公司的有限元分析软件HyperXtrude平台,对挤压模具强度进行有限元分析模拟技术,可以用于优化挤压模具厚度设计方案。优化设计的过程是可行的,优化结果是有效的,大大减少了试模次数。
c、试验结果表明:合理的选择模具厚度,及可以保证模具强度满足挤压需要,又可以有效的节约模具成本。
相关文章
- 2021-09-08BIM技术丛书Revit软件应用系列Autodesk Revit族详解 [
- 2021-09-08全国专业技术人员计算机应用能力考试用书 AutoCAD2004
- 2021-09-08EXCEL在工作中的应用 制表、数据处理及宏应用PDF下载
- 2021-08-30从零开始AutoCAD 2014中文版机械制图基础培训教程 [李
- 2021-08-30从零开始AutoCAD 2014中文版建筑制图基础培训教程 [朱
- 2021-08-30电气CAD实例教程AutoCAD 2010中文版 [左昉 等编著] 20
- 2021-08-30电影风暴2:Maya影像实拍与三维合成攻略PDF下载
- 2021-08-30高等院校艺术设计案例教程中文版AutoCAD 建筑设计案例
- 2021-08-29环境艺术制图AutoCAD [徐幼光 编著] 2013年PDF下载
- 2021-08-29机械AutoCAD 项目教程 第3版 [缪希伟 主编] 2012年PDF